How To Design Modular Homes
-
-
- Are modular homes cheaper? Often, yes, but not always drastically. Savings come from faster build time (less labour/financing cost), less material waste, and predictable pricing. The value for the quality is excellent.
-
- Do modular homes look different than a regular house? Not necessarily! Modern modular design offers incredible flexibility. They can look identical to any traditional home style, single-storey homes, colonial, cottage style homes, modern, or have a unique contemporary look. The key is the design chosen.
-
- Are modular homes as strong as regular homes? Yes, and often stronger. Modules must endure transportation stresses, requiring robust construction. Once bolted together on a permanent foundation, they form a very solid structure meeting all local building codes.
-
- How long does it take to build a modular home? The factory build might take 4-12 weeks per module (depending on size/complexity). Site prep and foundation work happen concurrently. Assembly on-site typically takes 1-4 weeks. Overall, it’s usually 30-50% faster than site-built.
-
- Can I customize a modular home? Absolutely! While manufacturers offer plans, customization is a major advantage of modern modular. Work with a modular builder/architect to design a home catered for specific needs, within transportation limits.
-
- What are the financing differences? Financing a modular home is very similar to financing a site-built home. You typically get a standard construction loan that converts to a permanent mortgage once the home is complete and certified. Some lenders specialise in modular construction loans.
-
- Do modular homes depreciate? No. Because they are built to local codes and placed on permanent foundations, modular homes appreciate in value over time, just like traditional site-built homes. This is different from manufactured (mobile) homes.
-
- What about resale value? Resale value is generally comparable to similar site-built homes in the same area. There is typically no distinction on property records or appraisals between a well-built modular home and a site-built home.
- Are there limitations on where I can build? The main limitations relate to transportation access. The route from the factory to the site must accommodate the large trucks and modules. Very narrow roads, low bridges, or steep, winding driveways can pose challenges that need planning. Local zoning rules also apply, just like any build.
-
[/vc_column_text][/vc_column][/vc_row]
- Complex Shapes: Clever design can combine modules at angles or use non-rectangular modules to create unique shapes that don’t look “boxy.”
In Conclusion
Modular home design offers a smart alternative to traditional building. It combines the efficiency and quality control of factory construction with the flexibility and permanence of site-built homes.
By designing the house as a set of interconnected modules built indoors, the process achieves significant advantages: faster construction times, predictable costs, high quality, and strong energy performance. Modern techniques ensure modular homes can be beautiful, customized, and built to last, meeting the same standards as any house on the block.
Frequently Asked Questions:
-
-
- Are modular homes cheaper? Often, yes, but not always drastically. Savings come from faster build time (less labour/financing cost), less material waste, and predictable pricing. The value for the quality is excellent.
-
- Do modular homes look different than a regular house? Not necessarily! Modern modular design offers incredible flexibility. They can look identical to any traditional home style, single-storey homes, colonial, cottage style homes, modern, or have a unique contemporary look. The key is the design chosen.
-
- Are modular homes as strong as regular homes? Yes, and often stronger. Modules must endure transportation stresses, requiring robust construction. Once bolted together on a permanent foundation, they form a very solid structure meeting all local building codes.
-
- How long does it take to build a modular home? The factory build might take 4-12 weeks per module (depending on size/complexity). Site prep and foundation work happen concurrently. Assembly on-site typically takes 1-4 weeks. Overall, it’s usually 30-50% faster than site-built.
-
- Can I customize a modular home? Absolutely! While manufacturers offer plans, customization is a major advantage of modern modular. Work with a modular builder/architect to design a home catered for specific needs, within transportation limits.
-
- What are the financing differences? Financing a modular home is very similar to financing a site-built home. You typically get a standard construction loan that converts to a permanent mortgage once the home is complete and certified. Some lenders specialise in modular construction loans.
-
- Do modular homes depreciate? No. Because they are built to local codes and placed on permanent foundations, modular homes appreciate in value over time, just like traditional site-built homes. This is different from manufactured (mobile) homes.
-
- What about resale value? Resale value is generally comparable to similar site-built homes in the same area. There is typically no distinction on property records or appraisals between a well-built modular home and a site-built home.
- Are there limitations on where I can build? The main limitations relate to transportation access. The route from the factory to the site must accommodate the large trucks and modules. Very narrow roads, low bridges, or steep, winding driveways can pose challenges that need planning. Local zoning rules also apply, just like any build.
-
[/vc_column_text][/vc_column][/vc_row]
- Complex Shapes: Clever design can combine modules at angles or use non-rectangular modules to create unique shapes that don’t look “boxy.”
In Conclusion
Modular home design offers a smart alternative to traditional building. It combines the efficiency and quality control of factory construction with the flexibility and permanence of site-built homes.
By designing the house as a set of interconnected modules built indoors, the process achieves significant advantages: faster construction times, predictable costs, high quality, and strong energy performance. Modern techniques ensure modular homes can be beautiful, customized, and built to last, meeting the same standards as any house on the block.
Frequently Asked Questions:
-
-
- Are modular homes cheaper? Often, yes, but not always drastically. Savings come from faster build time (less labour/financing cost), less material waste, and predictable pricing. The value for the quality is excellent.
-
- Do modular homes look different than a regular house? Not necessarily! Modern modular design offers incredible flexibility. They can look identical to any traditional home style, single-storey homes, colonial, cottage style homes, modern, or have a unique contemporary look. The key is the design chosen.
-
- Are modular homes as strong as regular homes? Yes, and often stronger. Modules must endure transportation stresses, requiring robust construction. Once bolted together on a permanent foundation, they form a very solid structure meeting all local building codes.
-
- How long does it take to build a modular home? The factory build might take 4-12 weeks per module (depending on size/complexity). Site prep and foundation work happen concurrently. Assembly on-site typically takes 1-4 weeks. Overall, it’s usually 30-50% faster than site-built.
-
- Can I customize a modular home? Absolutely! While manufacturers offer plans, customization is a major advantage of modern modular. Work with a modular builder/architect to design a home catered for specific needs, within transportation limits.
-
- What are the financing differences? Financing a modular home is very similar to financing a site-built home. You typically get a standard construction loan that converts to a permanent mortgage once the home is complete and certified. Some lenders specialise in modular construction loans.
-
- Do modular homes depreciate? No. Because they are built to local codes and placed on permanent foundations, modular homes appreciate in value over time, just like traditional site-built homes. This is different from manufactured (mobile) homes.
-
- What about resale value? Resale value is generally comparable to similar site-built homes in the same area. There is typically no distinction on property records or appraisals between a well-built modular home and a site-built home.
- Are there limitations on where I can build? The main limitations relate to transportation access. The route from the factory to the site must accommodate the large trucks and modules. Very narrow roads, low bridges, or steep, winding driveways can pose challenges that need planning. Local zoning rules also apply, just like any build.
-
[/vc_column_text][/vc_column][/vc_row]
-
-
- Modern Masterpieces: Architects use modules to create stunning, contemporary homes with clean lines, large windows, and open floor plans. Modules can be stacked creatively for multi-story designs.
-
- Charming Cottages: Compact and efficient, modular designs excel at creating cosy, well-designed smaller homes or vacation cabins.
-
- Expansive Family Homes: Large single-storey homes, colonials, and compact pitched-roof homes are commonly built modularly. Modules are joined side-by-side and sometimes stacked to create spacious living areas.
-
- Multi-Family Housing: Modular construction is highly efficient for building apartments, town homes, and student housing, offering speed and consistent quality.
-
- Accessory Dwelling Units (ADUs): Modular construction is ideal for backyard cottages or granny flats, providing a fast and less disruptive way to add living space.
- Complex Shapes: Clever design can combine modules at angles or use non-rectangular modules to create unique shapes that don’t look “boxy.”
-
In Conclusion
Modular home design offers a smart alternative to traditional building. It combines the efficiency and quality control of factory construction with the flexibility and permanence of site-built homes.
By designing the house as a set of interconnected modules built indoors, the process achieves significant advantages: faster construction times, predictable costs, high quality, and strong energy performance. Modern techniques ensure modular homes can be beautiful, customized, and built to last, meeting the same standards as any house on the block.
Frequently Asked Questions:
-
-
- Are modular homes cheaper? Often, yes, but not always drastically. Savings come from faster build time (less labour/financing cost), less material waste, and predictable pricing. The value for the quality is excellent.
-
- Do modular homes look different than a regular house? Not necessarily! Modern modular design offers incredible flexibility. They can look identical to any traditional home style, single-storey homes, colonial, cottage style homes, modern, or have a unique contemporary look. The key is the design chosen.
-
- Are modular homes as strong as regular homes? Yes, and often stronger. Modules must endure transportation stresses, requiring robust construction. Once bolted together on a permanent foundation, they form a very solid structure meeting all local building codes.
-
- How long does it take to build a modular home? The factory build might take 4-12 weeks per module (depending on size/complexity). Site prep and foundation work happen concurrently. Assembly on-site typically takes 1-4 weeks. Overall, it’s usually 30-50% faster than site-built.
-
- Can I customize a modular home? Absolutely! While manufacturers offer plans, customization is a major advantage of modern modular. Work with a modular builder/architect to design a home catered for specific needs, within transportation limits.
-
- What are the financing differences? Financing a modular home is very similar to financing a site-built home. You typically get a standard construction loan that converts to a permanent mortgage once the home is complete and certified. Some lenders specialise in modular construction loans.
-
- Do modular homes depreciate? No. Because they are built to local codes and placed on permanent foundations, modular homes appreciate in value over time, just like traditional site-built homes. This is different from manufactured (mobile) homes.
-
- What about resale value? Resale value is generally comparable to similar site-built homes in the same area. There is typically no distinction on property records or appraisals between a well-built modular home and a site-built home.
- Are there limitations on where I can build? The main limitations relate to transportation access. The route from the factory to the site must accommodate the large trucks and modules. Very narrow roads, low bridges, or steep, winding driveways can pose challenges that need planning. Local zoning rules also apply, just like any build.
-
[/vc_column_text][/vc_column][/vc_row]
Building ExamplesModular design isn’t limited to simple boxes. It can achieve remarkable results:
-
-
- Modern Masterpieces: Architects use modules to create stunning, contemporary homes with clean lines, large windows, and open floor plans. Modules can be stacked creatively for multi-story designs.
-
- Charming Cottages: Compact and efficient, modular designs excel at creating cosy, well-designed smaller homes or vacation cabins.
-
- Expansive Family Homes: Large single-storey homes, colonials, and compact pitched-roof homes are commonly built modularly. Modules are joined side-by-side and sometimes stacked to create spacious living areas.
-
- Multi-Family Housing: Modular construction is highly efficient for building apartments, town homes, and student housing, offering speed and consistent quality.
-
- Accessory Dwelling Units (ADUs): Modular construction is ideal for backyard cottages or granny flats, providing a fast and less disruptive way to add living space.
- Complex Shapes: Clever design can combine modules at angles or use non-rectangular modules to create unique shapes that don’t look “boxy.”
-
In Conclusion
Modular home design offers a smart alternative to traditional building. It combines the efficiency and quality control of factory construction with the flexibility and permanence of site-built homes.
By designing the house as a set of interconnected modules built indoors, the process achieves significant advantages: faster construction times, predictable costs, high quality, and strong energy performance. Modern techniques ensure modular homes can be beautiful, customized, and built to last, meeting the same standards as any house on the block.
Frequently Asked Questions:
-
-
- Are modular homes cheaper? Often, yes, but not always drastically. Savings come from faster build time (less labour/financing cost), less material waste, and predictable pricing. The value for the quality is excellent.
-
- Do modular homes look different than a regular house? Not necessarily! Modern modular design offers incredible flexibility. They can look identical to any traditional home style, single-storey homes, colonial, cottage style homes, modern, or have a unique contemporary look. The key is the design chosen.
-
- Are modular homes as strong as regular homes? Yes, and often stronger. Modules must endure transportation stresses, requiring robust construction. Once bolted together on a permanent foundation, they form a very solid structure meeting all local building codes.
-
- How long does it take to build a modular home? The factory build might take 4-12 weeks per module (depending on size/complexity). Site prep and foundation work happen concurrently. Assembly on-site typically takes 1-4 weeks. Overall, it’s usually 30-50% faster than site-built.
-
- Can I customize a modular home? Absolutely! While manufacturers offer plans, customization is a major advantage of modern modular. Work with a modular builder/architect to design a home catered for specific needs, within transportation limits.
-
- What are the financing differences? Financing a modular home is very similar to financing a site-built home. You typically get a standard construction loan that converts to a permanent mortgage once the home is complete and certified. Some lenders specialise in modular construction loans.
-
- Do modular homes depreciate? No. Because they are built to local codes and placed on permanent foundations, modular homes appreciate in value over time, just like traditional site-built homes. This is different from manufactured (mobile) homes.
-
- What about resale value? Resale value is generally comparable to similar site-built homes in the same area. There is typically no distinction on property records or appraisals between a well-built modular home and a site-built home.
- Are there limitations on where I can build? The main limitations relate to transportation access. The route from the factory to the site must accommodate the large trucks and modules. Very narrow roads, low bridges, or steep, winding driveways can pose challenges that need planning. Local zoning rules also apply, just like any build.
-
[/vc_column_text][/vc_column][/vc_row]
Once assembled, the home undergoes finishing touches. This may include flooring, light fittings, cabinet installations, and paint touch-ups. Then, a final inspection is done to ensure everything meets local building codes. At this point, the home is move-in ready.
Why choose modular? The advantages are compelling:
-
-
- Speed: This is a huge factor. Because factory work happens simultaneously with site prep, and bad weather doesn’t delay indoor construction, the overall build time is significantly faster; often 30-50% quicker than traditional building, that is assuming there are no delays in traditional building due to due to weather, labour shortages, or material supply issues. You move in sooner.
-
- Cost Efficiency: While the base price per square foot might be similar, modular building offers real savings. Faster construction means lower labour costs and financing costs. Less material waste in the controlled factory environment saves money. Predictable pricing is also easier to achieve.
-
- Quality Control: Building in a controlled factory environment is key. Materials are stored properly and protected from weather damage. Skilled workers follow precise processes with constant supervision. Consistent inspections throughout construction ensure high standards. This often results in a tighter, more energy-efficient building envelope.
-
- Scheduling Certainty: Factory production schedules are precise. Weather delays are mostly eliminated. This leads to much greater predictability for move-in dates.
-
- Design Flexibility: Forget the old stereotypes. Modern modular design is highly flexible. Architects can create custom designs, or you can choose from numerous plans offered by modular manufacturers. Styles range from traditional to ultra-modern.
-
- Strength: Modules are built to withstand the rigours of transportation. They must be lifted by a crane and travel on highways. This requires a resilient structure, often stronger than some site-built equivalents. Bolting them together creates a very solid home.
- Sustainability: The factory setting allows for better waste management and recycling of materials. Precise cutting reduces scrap. Tighter construction improves energy efficiency, lowering heating and cooling costs. Some factories also use sustainable materials.
-
Building Examples
Modular design isn’t limited to simple boxes. It can achieve remarkable results:
-
-
- Modern Masterpieces: Architects use modules to create stunning, contemporary homes with clean lines, large windows, and open floor plans. Modules can be stacked creatively for multi-story designs.
-
- Charming Cottages: Compact and efficient, modular designs excel at creating cosy, well-designed smaller homes or vacation cabins.
-
- Expansive Family Homes: Large single-storey homes, colonials, and compact pitched-roof homes are commonly built modularly. Modules are joined side-by-side and sometimes stacked to create spacious living areas.
-
- Multi-Family Housing: Modular construction is highly efficient for building apartments, town homes, and student housing, offering speed and consistent quality.
-
- Accessory Dwelling Units (ADUs): Modular construction is ideal for backyard cottages or granny flats, providing a fast and less disruptive way to add living space.
- Complex Shapes: Clever design can combine modules at angles or use non-rectangular modules to create unique shapes that don’t look “boxy.”
-
In Conclusion
Modular home design offers a smart alternative to traditional building. It combines the efficiency and quality control of factory construction with the flexibility and permanence of site-built homes.
By designing the house as a set of interconnected modules built indoors, the process achieves significant advantages: faster construction times, predictable costs, high quality, and strong energy performance. Modern techniques ensure modular homes can be beautiful, customized, and built to last, meeting the same standards as any house on the block.
Frequently Asked Questions:
-
-
- Are modular homes cheaper? Often, yes, but not always drastically. Savings come from faster build time (less labour/financing cost), less material waste, and predictable pricing. The value for the quality is excellent.
-
- Do modular homes look different than a regular house? Not necessarily! Modern modular design offers incredible flexibility. They can look identical to any traditional home style, single-storey homes, colonial, cottage style homes, modern, or have a unique contemporary look. The key is the design chosen.
-
- Are modular homes as strong as regular homes? Yes, and often stronger. Modules must endure transportation stresses, requiring robust construction. Once bolted together on a permanent foundation, they form a very solid structure meeting all local building codes.
-
- How long does it take to build a modular home? The factory build might take 4-12 weeks per module (depending on size/complexity). Site prep and foundation work happen concurrently. Assembly on-site typically takes 1-4 weeks. Overall, it’s usually 30-50% faster than site-built.
-
- Can I customize a modular home? Absolutely! While manufacturers offer plans, customization is a major advantage of modern modular. Work with a modular builder/architect to design a home catered for specific needs, within transportation limits.
-
- What are the financing differences? Financing a modular home is very similar to financing a site-built home. You typically get a standard construction loan that converts to a permanent mortgage once the home is complete and certified. Some lenders specialise in modular construction loans.
-
- Do modular homes depreciate? No. Because they are built to local codes and placed on permanent foundations, modular homes appreciate in value over time, just like traditional site-built homes. This is different from manufactured (mobile) homes.
-
- What about resale value? Resale value is generally comparable to similar site-built homes in the same area. There is typically no distinction on property records or appraisals between a well-built modular home and a site-built home.
- Are there limitations on where I can build? The main limitations relate to transportation access. The route from the factory to the site must accommodate the large trucks and modules. Very narrow roads, low bridges, or steep, winding driveways can pose challenges that need planning. Local zoning rules also apply, just like any build.
-
[/vc_column_text][/vc_column][/vc_row]
-
- Design & Engineering: This is the crucial first step. Architects and engineers work together, often using specialized software. They design the entire house, but broken down into transportable modules.
They determine:
- Design & Engineering: This is the crucial first step. Architects and engineers work together, often using specialized software. They design the entire house, but broken down into transportable modules.
-
-
- Module Size & Shape: How big can each box be to fit on a truck and navigate roads? (Usually max 16 feet wide, 60-70 feet long, but heights vary depending on country and region).
-
- Factory Workflow: How will the module move through the factory assembly line efficiently? What gets installed at each station?
- Approvals: Detailed plans are submitted for local building permits, just like a site-built home.
-
2. Factory Construction:
-
-
- Building the Box: Construction starts on a jig (a precise frame) ensuring perfect dimensions. The floor frame is built first.
-
- Walls Go Up: Exterior and interior walls are framed and stood up on the floor. Sheathing (the outer layer, like plywood) is applied.
-
- Roofing: The roof structure is built and often covered right there in the factory.
-
- Utilities Rough-In: Plumbing pipes and electrical wires are installed inside the walls, floors, and ceilings. HVAC ductwork may also be installed.
-
- Insulation: High-quality insulation is carefully placed in all walls, floors, and ceilings.
-
- Drywall: Interior walls and ceilings get covered with drywall, which is taped, mudded, and sanded smooth.
-
- Interior Finishes: Priming, painting, installing cabinets, countertops, flooring, trim, doors, and even bathroom fixtures often happen in the factory. Appliances might be installed or prepped.
-
- Quality Control: Rigorous inspections happen throughout the process. The finished module is checked against plans.
- Weather Protection: Modules are wrapped tightly for transport to protect against weather and road debris.
-
In many cases, 70–90% of the home is completed before it even leaves the factory.
3. Transportation & Site Prep: While modules are built, the building site is prepared. The foundation (basement, crawl space, or slab) is constructed and inspected. Simultaneously, specialized trucks transport the modules, one or two at a time, to the site. This requires careful route planning.
Proper site preparation ensures that when the modules arrive, everything can be fitted quickly and securely.
4. Crane & Set: A large crane lifts each module off the truck and carefully places it onto the foundation. This is a dramatic and precise operation.
5. Assembly & Finishing:
-
-
- Joining Modules: Modules are bolted together structurally. The roof sections are joined.
-
- Sealing Joints: The seams where modules meet (both inside and outside) are meticulously sealed and flashed to make them weathertight and invisible.
-
- Utility Connections: Electricians and plumbers connect the wiring and plumbing between modules and hook up to the main utilities (septic/sewer, water, electricity, gas).
- HVAC Connections: Ductwork sections between modules are connected, and the system is tested. Skilled workers then handle the sealing, joining, and alignment. This stage is fast; some homes are assembled in just a few days.
-
6. Final Finishes and Inspection
Once assembled, the home undergoes finishing touches. This may include flooring, light fittings, cabinet installations, and paint touch-ups. Then, a final inspection is done to ensure everything meets local building codes. At this point, the home is move-in ready.
Why choose modular? The advantages are compelling:
-
-
- Speed: This is a huge factor. Because factory work happens simultaneously with site prep, and bad weather doesn’t delay indoor construction, the overall build time is significantly faster; often 30-50% quicker than traditional building, that is assuming there are no delays in traditional building due to due to weather, labour shortages, or material supply issues. You move in sooner.
-
- Cost Efficiency: While the base price per square foot might be similar, modular building offers real savings. Faster construction means lower labour costs and financing costs. Less material waste in the controlled factory environment saves money. Predictable pricing is also easier to achieve.
-
- Quality Control: Building in a controlled factory environment is key. Materials are stored properly and protected from weather damage. Skilled workers follow precise processes with constant supervision. Consistent inspections throughout construction ensure high standards. This often results in a tighter, more energy-efficient building envelope.
-
- Scheduling Certainty: Factory production schedules are precise. Weather delays are mostly eliminated. This leads to much greater predictability for move-in dates.
-
- Design Flexibility: Forget the old stereotypes. Modern modular design is highly flexible. Architects can create custom designs, or you can choose from numerous plans offered by modular manufacturers. Styles range from traditional to ultra-modern.
-
- Strength: Modules are built to withstand the rigours of transportation. They must be lifted by a crane and travel on highways. This requires a resilient structure, often stronger than some site-built equivalents. Bolting them together creates a very solid home.
- Sustainability: The factory setting allows for better waste management and recycling of materials. Precise cutting reduces scrap. Tighter construction improves energy efficiency, lowering heating and cooling costs. Some factories also use sustainable materials.
-
Building Examples
Modular design isn’t limited to simple boxes. It can achieve remarkable results:
-
-
- Modern Masterpieces: Architects use modules to create stunning, contemporary homes with clean lines, large windows, and open floor plans. Modules can be stacked creatively for multi-story designs.
-
- Charming Cottages: Compact and efficient, modular designs excel at creating cosy, well-designed smaller homes or vacation cabins.
-
- Expansive Family Homes: Large single-storey homes, colonials, and compact pitched-roof homes are commonly built modularly. Modules are joined side-by-side and sometimes stacked to create spacious living areas.
-
- Multi-Family Housing: Modular construction is highly efficient for building apartments, town homes, and student housing, offering speed and consistent quality.
-
- Accessory Dwelling Units (ADUs): Modular construction is ideal for backyard cottages or granny flats, providing a fast and less disruptive way to add living space.
- Complex Shapes: Clever design can combine modules at angles or use non-rectangular modules to create unique shapes that don’t look “boxy.”
-
In Conclusion
Modular home design offers a smart alternative to traditional building. It combines the efficiency and quality control of factory construction with the flexibility and permanence of site-built homes.
By designing the house as a set of interconnected modules built indoors, the process achieves significant advantages: faster construction times, predictable costs, high quality, and strong energy performance. Modern techniques ensure modular homes can be beautiful, customized, and built to last, meeting the same standards as any house on the block.
Frequently Asked Questions:
-
-
- Are modular homes cheaper? Often, yes, but not always drastically. Savings come from faster build time (less labour/financing cost), less material waste, and predictable pricing. The value for the quality is excellent.
-
- Do modular homes look different than a regular house? Not necessarily! Modern modular design offers incredible flexibility. They can look identical to any traditional home style, single-storey homes, colonial, cottage style homes, modern, or have a unique contemporary look. The key is the design chosen.
-
- Are modular homes as strong as regular homes? Yes, and often stronger. Modules must endure transportation stresses, requiring robust construction. Once bolted together on a permanent foundation, they form a very solid structure meeting all local building codes.
-
- How long does it take to build a modular home? The factory build might take 4-12 weeks per module (depending on size/complexity). Site prep and foundation work happen concurrently. Assembly on-site typically takes 1-4 weeks. Overall, it’s usually 30-50% faster than site-built.
-
- Can I customize a modular home? Absolutely! While manufacturers offer plans, customization is a major advantage of modern modular. Work with a modular builder/architect to design a home catered for specific needs, within transportation limits.
-
- What are the financing differences? Financing a modular home is very similar to financing a site-built home. You typically get a standard construction loan that converts to a permanent mortgage once the home is complete and certified. Some lenders specialise in modular construction loans.
-
- Do modular homes depreciate? No. Because they are built to local codes and placed on permanent foundations, modular homes appreciate in value over time, just like traditional site-built homes. This is different from manufactured (mobile) homes.
-
- What about resale value? Resale value is generally comparable to similar site-built homes in the same area. There is typically no distinction on property records or appraisals between a well-built modular home and a site-built home.
- Are there limitations on where I can build? The main limitations relate to transportation access. The route from the factory to the site must accommodate the large trucks and modules. Very narrow roads, low bridges, or steep, winding driveways can pose challenges that need planning. Local zoning rules also apply, just like any build.
-
[/vc_column_text][/vc_column][/vc_row]
Understanding how a modular home is built helps explain the design needs. Here’s the typical journey:-
- Design & Engineering: This is the crucial first step. Architects and engineers work together, often using specialized software. They design the entire house, but broken down into transportable modules.
They determine:
- Design & Engineering: This is the crucial first step. Architects and engineers work together, often using specialized software. They design the entire house, but broken down into transportable modules.
-
-
- Module Size & Shape: How big can each box be to fit on a truck and navigate roads? (Usually max 16 feet wide, 60-70 feet long, but heights vary depending on country and region).
-
- Factory Workflow: How will the module move through the factory assembly line efficiently? What gets installed at each station?
- Approvals: Detailed plans are submitted for local building permits, just like a site-built home.
-
2. Factory Construction:
-
-
- Building the Box: Construction starts on a jig (a precise frame) ensuring perfect dimensions. The floor frame is built first.
-
- Walls Go Up: Exterior and interior walls are framed and stood up on the floor. Sheathing (the outer layer, like plywood) is applied.
-
- Roofing: The roof structure is built and often covered right there in the factory.
-
- Utilities Rough-In: Plumbing pipes and electrical wires are installed inside the walls, floors, and ceilings. HVAC ductwork may also be installed.
-
- Insulation: High-quality insulation is carefully placed in all walls, floors, and ceilings.
-
- Drywall: Interior walls and ceilings get covered with drywall, which is taped, mudded, and sanded smooth.
-
- Interior Finishes: Priming, painting, installing cabinets, countertops, flooring, trim, doors, and even bathroom fixtures often happen in the factory. Appliances might be installed or prepped.
-
- Quality Control: Rigorous inspections happen throughout the process. The finished module is checked against plans.
- Weather Protection: Modules are wrapped tightly for transport to protect against weather and road debris.
-
In many cases, 70–90% of the home is completed before it even leaves the factory.
3. Transportation & Site Prep: While modules are built, the building site is prepared. The foundation (basement, crawl space, or slab) is constructed and inspected. Simultaneously, specialized trucks transport the modules, one or two at a time, to the site. This requires careful route planning.
Proper site preparation ensures that when the modules arrive, everything can be fitted quickly and securely.
4. Crane & Set: A large crane lifts each module off the truck and carefully places it onto the foundation. This is a dramatic and precise operation.
5. Assembly & Finishing:
-
-
- Joining Modules: Modules are bolted together structurally. The roof sections are joined.
-
- Sealing Joints: The seams where modules meet (both inside and outside) are meticulously sealed and flashed to make them weathertight and invisible.
-
- Utility Connections: Electricians and plumbers connect the wiring and plumbing between modules and hook up to the main utilities (septic/sewer, water, electricity, gas).
- HVAC Connections: Ductwork sections between modules are connected, and the system is tested. Skilled workers then handle the sealing, joining, and alignment. This stage is fast; some homes are assembled in just a few days.
-
6. Final Finishes and Inspection
Once assembled, the home undergoes finishing touches. This may include flooring, light fittings, cabinet installations, and paint touch-ups. Then, a final inspection is done to ensure everything meets local building codes. At this point, the home is move-in ready.
Why choose modular? The advantages are compelling:
-
-
- Speed: This is a huge factor. Because factory work happens simultaneously with site prep, and bad weather doesn’t delay indoor construction, the overall build time is significantly faster; often 30-50% quicker than traditional building, that is assuming there are no delays in traditional building due to due to weather, labour shortages, or material supply issues. You move in sooner.
-
- Cost Efficiency: While the base price per square foot might be similar, modular building offers real savings. Faster construction means lower labour costs and financing costs. Less material waste in the controlled factory environment saves money. Predictable pricing is also easier to achieve.
-
- Quality Control: Building in a controlled factory environment is key. Materials are stored properly and protected from weather damage. Skilled workers follow precise processes with constant supervision. Consistent inspections throughout construction ensure high standards. This often results in a tighter, more energy-efficient building envelope.
-
- Scheduling Certainty: Factory production schedules are precise. Weather delays are mostly eliminated. This leads to much greater predictability for move-in dates.
-
- Design Flexibility: Forget the old stereotypes. Modern modular design is highly flexible. Architects can create custom designs, or you can choose from numerous plans offered by modular manufacturers. Styles range from traditional to ultra-modern.
-
- Strength: Modules are built to withstand the rigours of transportation. They must be lifted by a crane and travel on highways. This requires a resilient structure, often stronger than some site-built equivalents. Bolting them together creates a very solid home.
- Sustainability: The factory setting allows for better waste management and recycling of materials. Precise cutting reduces scrap. Tighter construction improves energy efficiency, lowering heating and cooling costs. Some factories also use sustainable materials.
-
Building Examples
Modular design isn’t limited to simple boxes. It can achieve remarkable results:
-
-
- Modern Masterpieces: Architects use modules to create stunning, contemporary homes with clean lines, large windows, and open floor plans. Modules can be stacked creatively for multi-story designs.
-
- Charming Cottages: Compact and efficient, modular designs excel at creating cosy, well-designed smaller homes or vacation cabins.
-
- Expansive Family Homes: Large single-storey homes, colonials, and compact pitched-roof homes are commonly built modularly. Modules are joined side-by-side and sometimes stacked to create spacious living areas.
-
- Multi-Family Housing: Modular construction is highly efficient for building apartments, town homes, and student housing, offering speed and consistent quality.
-
- Accessory Dwelling Units (ADUs): Modular construction is ideal for backyard cottages or granny flats, providing a fast and less disruptive way to add living space.
- Complex Shapes: Clever design can combine modules at angles or use non-rectangular modules to create unique shapes that don’t look “boxy.”
-
In Conclusion
Modular home design offers a smart alternative to traditional building. It combines the efficiency and quality control of factory construction with the flexibility and permanence of site-built homes.
By designing the house as a set of interconnected modules built indoors, the process achieves significant advantages: faster construction times, predictable costs, high quality, and strong energy performance. Modern techniques ensure modular homes can be beautiful, customized, and built to last, meeting the same standards as any house on the block.
Frequently Asked Questions:
-
-
- Are modular homes cheaper? Often, yes, but not always drastically. Savings come from faster build time (less labour/financing cost), less material waste, and predictable pricing. The value for the quality is excellent.
-
- Do modular homes look different than a regular house? Not necessarily! Modern modular design offers incredible flexibility. They can look identical to any traditional home style, single-storey homes, colonial, cottage style homes, modern, or have a unique contemporary look. The key is the design chosen.
-
- Are modular homes as strong as regular homes? Yes, and often stronger. Modules must endure transportation stresses, requiring robust construction. Once bolted together on a permanent foundation, they form a very solid structure meeting all local building codes.
-
- How long does it take to build a modular home? The factory build might take 4-12 weeks per module (depending on size/complexity). Site prep and foundation work happen concurrently. Assembly on-site typically takes 1-4 weeks. Overall, it’s usually 30-50% faster than site-built.
-
- Can I customize a modular home? Absolutely! While manufacturers offer plans, customization is a major advantage of modern modular. Work with a modular builder/architect to design a home catered for specific needs, within transportation limits.
-
- What are the financing differences? Financing a modular home is very similar to financing a site-built home. You typically get a standard construction loan that converts to a permanent mortgage once the home is complete and certified. Some lenders specialise in modular construction loans.
-
- Do modular homes depreciate? No. Because they are built to local codes and placed on permanent foundations, modular homes appreciate in value over time, just like traditional site-built homes. This is different from manufactured (mobile) homes.
-
- What about resale value? Resale value is generally comparable to similar site-built homes in the same area. There is typically no distinction on property records or appraisals between a well-built modular home and a site-built home.
- Are there limitations on where I can build? The main limitations relate to transportation access. The route from the factory to the site must accommodate the large trucks and modules. Very narrow roads, low bridges, or steep, winding driveways can pose challenges that need planning. Local zoning rules also apply, just like any build.
-
[/vc_column_text][/vc_column][/vc_row]
Understanding how a modular home is built helps explain the design needs. Here’s the typical journey:
-
- Design & Engineering: This is the crucial first step. Architects and engineers work together, often using specialized software. They design the entire house, but broken down into transportable modules.
They determine:
- Design & Engineering: This is the crucial first step. Architects and engineers work together, often using specialized software. They design the entire house, but broken down into transportable modules.
-
-
- Module Size & Shape: How big can each box be to fit on a truck and navigate roads? (Usually max 16 feet wide, 60-70 feet long, but heights vary depending on country and region).
-
- Factory Workflow: How will the module move through the factory assembly line efficiently? What gets installed at each station?
- Approvals: Detailed plans are submitted for local building permits, just like a site-built home.
-
2. Factory Construction:
-
-
- Building the Box: Construction starts on a jig (a precise frame) ensuring perfect dimensions. The floor frame is built first.
-
- Walls Go Up: Exterior and interior walls are framed and stood up on the floor. Sheathing (the outer layer, like plywood) is applied.
-
- Roofing: The roof structure is built and often covered right there in the factory.
-
- Utilities Rough-In: Plumbing pipes and electrical wires are installed inside the walls, floors, and ceilings. HVAC ductwork may also be installed.
-
- Insulation: High-quality insulation is carefully placed in all walls, floors, and ceilings.
-
- Drywall: Interior walls and ceilings get covered with drywall, which is taped, mudded, and sanded smooth.
-
- Interior Finishes: Priming, painting, installing cabinets, countertops, flooring, trim, doors, and even bathroom fixtures often happen in the factory. Appliances might be installed or prepped.
-
- Quality Control: Rigorous inspections happen throughout the process. The finished module is checked against plans.
- Weather Protection: Modules are wrapped tightly for transport to protect against weather and road debris.
-
In many cases, 70–90% of the home is completed before it even leaves the factory.
3. Transportation & Site Prep: While modules are built, the building site is prepared. The foundation (basement, crawl space, or slab) is constructed and inspected. Simultaneously, specialized trucks transport the modules, one or two at a time, to the site. This requires careful route planning.
Proper site preparation ensures that when the modules arrive, everything can be fitted quickly and securely.
4. Crane & Set: A large crane lifts each module off the truck and carefully places it onto the foundation. This is a dramatic and precise operation.
5. Assembly & Finishing:
-
-
- Joining Modules: Modules are bolted together structurally. The roof sections are joined.
-
- Sealing Joints: The seams where modules meet (both inside and outside) are meticulously sealed and flashed to make them weathertight and invisible.
-
- Utility Connections: Electricians and plumbers connect the wiring and plumbing between modules and hook up to the main utilities (septic/sewer, water, electricity, gas).
- HVAC Connections: Ductwork sections between modules are connected, and the system is tested. Skilled workers then handle the sealing, joining, and alignment. This stage is fast; some homes are assembled in just a few days.
-
6. Final Finishes and Inspection
Once assembled, the home undergoes finishing touches. This may include flooring, light fittings, cabinet installations, and paint touch-ups. Then, a final inspection is done to ensure everything meets local building codes. At this point, the home is move-in ready.
Why choose modular? The advantages are compelling:
-
-
- Speed: This is a huge factor. Because factory work happens simultaneously with site prep, and bad weather doesn’t delay indoor construction, the overall build time is significantly faster; often 30-50% quicker than traditional building, that is assuming there are no delays in traditional building due to due to weather, labour shortages, or material supply issues. You move in sooner.
-
- Cost Efficiency: While the base price per square foot might be similar, modular building offers real savings. Faster construction means lower labour costs and financing costs. Less material waste in the controlled factory environment saves money. Predictable pricing is also easier to achieve.
-
- Quality Control: Building in a controlled factory environment is key. Materials are stored properly and protected from weather damage. Skilled workers follow precise processes with constant supervision. Consistent inspections throughout construction ensure high standards. This often results in a tighter, more energy-efficient building envelope.
-
- Scheduling Certainty: Factory production schedules are precise. Weather delays are mostly eliminated. This leads to much greater predictability for move-in dates.
-
- Design Flexibility: Forget the old stereotypes. Modern modular design is highly flexible. Architects can create custom designs, or you can choose from numerous plans offered by modular manufacturers. Styles range from traditional to ultra-modern.
-
- Strength: Modules are built to withstand the rigours of transportation. They must be lifted by a crane and travel on highways. This requires a resilient structure, often stronger than some site-built equivalents. Bolting them together creates a very solid home.
- Sustainability: The factory setting allows for better waste management and recycling of materials. Precise cutting reduces scrap. Tighter construction improves energy efficiency, lowering heating and cooling costs. Some factories also use sustainable materials.
-
Building Examples
Modular design isn’t limited to simple boxes. It can achieve remarkable results:
-
-
- Modern Masterpieces: Architects use modules to create stunning, contemporary homes with clean lines, large windows, and open floor plans. Modules can be stacked creatively for multi-story designs.
-
- Charming Cottages: Compact and efficient, modular designs excel at creating cosy, well-designed smaller homes or vacation cabins.
-
- Expansive Family Homes: Large single-storey homes, colonials, and compact pitched-roof homes are commonly built modularly. Modules are joined side-by-side and sometimes stacked to create spacious living areas.
-
- Multi-Family Housing: Modular construction is highly efficient for building apartments, town homes, and student housing, offering speed and consistent quality.
-
- Accessory Dwelling Units (ADUs): Modular construction is ideal for backyard cottages or granny flats, providing a fast and less disruptive way to add living space.
- Complex Shapes: Clever design can combine modules at angles or use non-rectangular modules to create unique shapes that don’t look “boxy.”
-
In Conclusion
Modular home design offers a smart alternative to traditional building. It combines the efficiency and quality control of factory construction with the flexibility and permanence of site-built homes.
By designing the house as a set of interconnected modules built indoors, the process achieves significant advantages: faster construction times, predictable costs, high quality, and strong energy performance. Modern techniques ensure modular homes can be beautiful, customized, and built to last, meeting the same standards as any house on the block.
Frequently Asked Questions:
-
-
- Are modular homes cheaper? Often, yes, but not always drastically. Savings come from faster build time (less labour/financing cost), less material waste, and predictable pricing. The value for the quality is excellent.
-
- Do modular homes look different than a regular house? Not necessarily! Modern modular design offers incredible flexibility. They can look identical to any traditional home style, single-storey homes, colonial, cottage style homes, modern, or have a unique contemporary look. The key is the design chosen.
-
- Are modular homes as strong as regular homes? Yes, and often stronger. Modules must endure transportation stresses, requiring robust construction. Once bolted together on a permanent foundation, they form a very solid structure meeting all local building codes.
-
- How long does it take to build a modular home? The factory build might take 4-12 weeks per module (depending on size/complexity). Site prep and foundation work happen concurrently. Assembly on-site typically takes 1-4 weeks. Overall, it’s usually 30-50% faster than site-built.
-
- Can I customize a modular home? Absolutely! While manufacturers offer plans, customization is a major advantage of modern modular. Work with a modular builder/architect to design a home catered for specific needs, within transportation limits.
-
- What are the financing differences? Financing a modular home is very similar to financing a site-built home. You typically get a standard construction loan that converts to a permanent mortgage once the home is complete and certified. Some lenders specialise in modular construction loans.
-
- Do modular homes depreciate? No. Because they are built to local codes and placed on permanent foundations, modular homes appreciate in value over time, just like traditional site-built homes. This is different from manufactured (mobile) homes.
-
- What about resale value? Resale value is generally comparable to similar site-built homes in the same area. There is typically no distinction on property records or appraisals between a well-built modular home and a site-built home.
- Are there limitations on where I can build? The main limitations relate to transportation access. The route from the factory to the site must accommodate the large trucks and modules. Very narrow roads, low bridges, or steep, winding driveways can pose challenges that need planning. Local zoning rules also apply, just like any build.
-
[/vc_column_text][/vc_column][/vc_row]
- Appreciation: Because they meet local codes and are on permanent foundations, modular homes appreciate in value similarly to site-built homes. Manufactured homes typically depreciate, like vehicles.
Construction Process of Modular Homes
Understanding how a modular home is built helps explain the design needs. Here’s the typical journey:
-
- Design & Engineering: This is the crucial first step. Architects and engineers work together, often using specialized software. They design the entire house, but broken down into transportable modules.
They determine:
- Design & Engineering: This is the crucial first step. Architects and engineers work together, often using specialized software. They design the entire house, but broken down into transportable modules.
-
-
- Module Size & Shape: How big can each box be to fit on a truck and navigate roads? (Usually max 16 feet wide, 60-70 feet long, but heights vary depending on country and region).
-
- Factory Workflow: How will the module move through the factory assembly line efficiently? What gets installed at each station?
- Approvals: Detailed plans are submitted for local building permits, just like a site-built home.
-
2. Factory Construction:
-
-
- Building the Box: Construction starts on a jig (a precise frame) ensuring perfect dimensions. The floor frame is built first.
-
- Walls Go Up: Exterior and interior walls are framed and stood up on the floor. Sheathing (the outer layer, like plywood) is applied.
-
- Roofing: The roof structure is built and often covered right there in the factory.
-
- Utilities Rough-In: Plumbing pipes and electrical wires are installed inside the walls, floors, and ceilings. HVAC ductwork may also be installed.
-
- Insulation: High-quality insulation is carefully placed in all walls, floors, and ceilings.
-
- Drywall: Interior walls and ceilings get covered with drywall, which is taped, mudded, and sanded smooth.
-
- Interior Finishes: Priming, painting, installing cabinets, countertops, flooring, trim, doors, and even bathroom fixtures often happen in the factory. Appliances might be installed or prepped.
-
- Quality Control: Rigorous inspections happen throughout the process. The finished module is checked against plans.
- Weather Protection: Modules are wrapped tightly for transport to protect against weather and road debris.
-
In many cases, 70–90% of the home is completed before it even leaves the factory.
3. Transportation & Site Prep: While modules are built, the building site is prepared. The foundation (basement, crawl space, or slab) is constructed and inspected. Simultaneously, specialized trucks transport the modules, one or two at a time, to the site. This requires careful route planning.
Proper site preparation ensures that when the modules arrive, everything can be fitted quickly and securely.
4. Crane & Set: A large crane lifts each module off the truck and carefully places it onto the foundation. This is a dramatic and precise operation.
5. Assembly & Finishing:
-
-
- Joining Modules: Modules are bolted together structurally. The roof sections are joined.
-
- Sealing Joints: The seams where modules meet (both inside and outside) are meticulously sealed and flashed to make them weathertight and invisible.
-
- Utility Connections: Electricians and plumbers connect the wiring and plumbing between modules and hook up to the main utilities (septic/sewer, water, electricity, gas).
- HVAC Connections: Ductwork sections between modules are connected, and the system is tested. Skilled workers then handle the sealing, joining, and alignment. This stage is fast; some homes are assembled in just a few days.
-
6. Final Finishes and Inspection
Once assembled, the home undergoes finishing touches. This may include flooring, light fittings, cabinet installations, and paint touch-ups. Then, a final inspection is done to ensure everything meets local building codes. At this point, the home is move-in ready.
Why choose modular? The advantages are compelling:
-
-
- Speed: This is a huge factor. Because factory work happens simultaneously with site prep, and bad weather doesn’t delay indoor construction, the overall build time is significantly faster; often 30-50% quicker than traditional building, that is assuming there are no delays in traditional building due to due to weather, labour shortages, or material supply issues. You move in sooner.
-
- Cost Efficiency: While the base price per square foot might be similar, modular building offers real savings. Faster construction means lower labour costs and financing costs. Less material waste in the controlled factory environment saves money. Predictable pricing is also easier to achieve.
-
- Quality Control: Building in a controlled factory environment is key. Materials are stored properly and protected from weather damage. Skilled workers follow precise processes with constant supervision. Consistent inspections throughout construction ensure high standards. This often results in a tighter, more energy-efficient building envelope.
-
- Scheduling Certainty: Factory production schedules are precise. Weather delays are mostly eliminated. This leads to much greater predictability for move-in dates.
-
- Design Flexibility: Forget the old stereotypes. Modern modular design is highly flexible. Architects can create custom designs, or you can choose from numerous plans offered by modular manufacturers. Styles range from traditional to ultra-modern.
-
- Strength: Modules are built to withstand the rigours of transportation. They must be lifted by a crane and travel on highways. This requires a resilient structure, often stronger than some site-built equivalents. Bolting them together creates a very solid home.
- Sustainability: The factory setting allows for better waste management and recycling of materials. Precise cutting reduces scrap. Tighter construction improves energy efficiency, lowering heating and cooling costs. Some factories also use sustainable materials.
-
Building Examples
Modular design isn’t limited to simple boxes. It can achieve remarkable results:
-
-
- Modern Masterpieces: Architects use modules to create stunning, contemporary homes with clean lines, large windows, and open floor plans. Modules can be stacked creatively for multi-story designs.
-
- Charming Cottages: Compact and efficient, modular designs excel at creating cosy, well-designed smaller homes or vacation cabins.
-
- Expansive Family Homes: Large single-storey homes, colonials, and compact pitched-roof homes are commonly built modularly. Modules are joined side-by-side and sometimes stacked to create spacious living areas.
-
- Multi-Family Housing: Modular construction is highly efficient for building apartments, town homes, and student housing, offering speed and consistent quality.
-
- Accessory Dwelling Units (ADUs): Modular construction is ideal for backyard cottages or granny flats, providing a fast and less disruptive way to add living space.
- Complex Shapes: Clever design can combine modules at angles or use non-rectangular modules to create unique shapes that don’t look “boxy.”
-
In Conclusion
Modular home design offers a smart alternative to traditional building. It combines the efficiency and quality control of factory construction with the flexibility and permanence of site-built homes.
By designing the house as a set of interconnected modules built indoors, the process achieves significant advantages: faster construction times, predictable costs, high quality, and strong energy performance. Modern techniques ensure modular homes can be beautiful, customized, and built to last, meeting the same standards as any house on the block.
Frequently Asked Questions:
-
-
- Are modular homes cheaper? Often, yes, but not always drastically. Savings come from faster build time (less labour/financing cost), less material waste, and predictable pricing. The value for the quality is excellent.
-
- Do modular homes look different than a regular house? Not necessarily! Modern modular design offers incredible flexibility. They can look identical to any traditional home style, single-storey homes, colonial, cottage style homes, modern, or have a unique contemporary look. The key is the design chosen.
-
- Are modular homes as strong as regular homes? Yes, and often stronger. Modules must endure transportation stresses, requiring robust construction. Once bolted together on a permanent foundation, they form a very solid structure meeting all local building codes.
-
- How long does it take to build a modular home? The factory build might take 4-12 weeks per module (depending on size/complexity). Site prep and foundation work happen concurrently. Assembly on-site typically takes 1-4 weeks. Overall, it’s usually 30-50% faster than site-built.
-
- Can I customize a modular home? Absolutely! While manufacturers offer plans, customization is a major advantage of modern modular. Work with a modular builder/architect to design a home catered for specific needs, within transportation limits.
-
- What are the financing differences? Financing a modular home is very similar to financing a site-built home. You typically get a standard construction loan that converts to a permanent mortgage once the home is complete and certified. Some lenders specialise in modular construction loans.
-
- Do modular homes depreciate? No. Because they are built to local codes and placed on permanent foundations, modular homes appreciate in value over time, just like traditional site-built homes. This is different from manufactured (mobile) homes.
-
- What about resale value? Resale value is generally comparable to similar site-built homes in the same area. There is typically no distinction on property records or appraisals between a well-built modular home and a site-built home.
- Are there limitations on where I can build? The main limitations relate to transportation access. The route from the factory to the site must accommodate the large trucks and modules. Very narrow roads, low bridges, or steep, winding driveways can pose challenges that need planning. Local zoning rules also apply, just like any build.
-
[/vc_column_text][/vc_column][/vc_row]
- Appreciation: Because they meet local codes and are on permanent foundations, modular homes appreciate in value similarly to site-built homes. Manufactured homes typically depreciate, like vehicles.
Construction Process of Modular Homes
Understanding how a modular home is built helps explain the design needs. Here’s the typical journey:
-
- Design & Engineering: This is the crucial first step. Architects and engineers work together, often using specialized software. They design the entire house, but broken down into transportable modules.
They determine:
- Design & Engineering: This is the crucial first step. Architects and engineers work together, often using specialized software. They design the entire house, but broken down into transportable modules.
-
-
- Module Size & Shape: How big can each box be to fit on a truck and navigate roads? (Usually max 16 feet wide, 60-70 feet long, but heights vary depending on country and region).
-
- Factory Workflow: How will the module move through the factory assembly line efficiently? What gets installed at each station?
- Approvals: Detailed plans are submitted for local building permits, just like a site-built home.
-
2. Factory Construction:
-
-
- Building the Box: Construction starts on a jig (a precise frame) ensuring perfect dimensions. The floor frame is built first.
-
- Walls Go Up: Exterior and interior walls are framed and stood up on the floor. Sheathing (the outer layer, like plywood) is applied.
-
- Roofing: The roof structure is built and often covered right there in the factory.
-
- Utilities Rough-In: Plumbing pipes and electrical wires are installed inside the walls, floors, and ceilings. HVAC ductwork may also be installed.
-
- Insulation: High-quality insulation is carefully placed in all walls, floors, and ceilings.
-
- Drywall: Interior walls and ceilings get covered with drywall, which is taped, mudded, and sanded smooth.
-
- Interior Finishes: Priming, painting, installing cabinets, countertops, flooring, trim, doors, and even bathroom fixtures often happen in the factory. Appliances might be installed or prepped.
-
- Quality Control: Rigorous inspections happen throughout the process. The finished module is checked against plans.
- Weather Protection: Modules are wrapped tightly for transport to protect against weather and road debris.
-
In many cases, 70–90% of the home is completed before it even leaves the factory.
3. Transportation & Site Prep: While modules are built, the building site is prepared. The foundation (basement, crawl space, or slab) is constructed and inspected. Simultaneously, specialized trucks transport the modules, one or two at a time, to the site. This requires careful route planning.
Proper site preparation ensures that when the modules arrive, everything can be fitted quickly and securely.
4. Crane & Set: A large crane lifts each module off the truck and carefully places it onto the foundation. This is a dramatic and precise operation.
5. Assembly & Finishing:
-
-
- Joining Modules: Modules are bolted together structurally. The roof sections are joined.
-
- Sealing Joints: The seams where modules meet (both inside and outside) are meticulously sealed and flashed to make them weathertight and invisible.
-
- Utility Connections: Electricians and plumbers connect the wiring and plumbing between modules and hook up to the main utilities (septic/sewer, water, electricity, gas).
- HVAC Connections: Ductwork sections between modules are connected, and the system is tested. Skilled workers then handle the sealing, joining, and alignment. This stage is fast; some homes are assembled in just a few days.
-
6. Final Finishes and Inspection
Once assembled, the home undergoes finishing touches. This may include flooring, light fittings, cabinet installations, and paint touch-ups. Then, a final inspection is done to ensure everything meets local building codes. At this point, the home is move-in ready.
Why choose modular? The advantages are compelling:
-
-
- Speed: This is a huge factor. Because factory work happens simultaneously with site prep, and bad weather doesn’t delay indoor construction, the overall build time is significantly faster; often 30-50% quicker than traditional building, that is assuming there are no delays in traditional building due to due to weather, labour shortages, or material supply issues. You move in sooner.
-
- Cost Efficiency: While the base price per square foot might be similar, modular building offers real savings. Faster construction means lower labour costs and financing costs. Less material waste in the controlled factory environment saves money. Predictable pricing is also easier to achieve.
-
- Quality Control: Building in a controlled factory environment is key. Materials are stored properly and protected from weather damage. Skilled workers follow precise processes with constant supervision. Consistent inspections throughout construction ensure high standards. This often results in a tighter, more energy-efficient building envelope.
-
- Scheduling Certainty: Factory production schedules are precise. Weather delays are mostly eliminated. This leads to much greater predictability for move-in dates.
-
- Design Flexibility: Forget the old stereotypes. Modern modular design is highly flexible. Architects can create custom designs, or you can choose from numerous plans offered by modular manufacturers. Styles range from traditional to ultra-modern.
-
- Strength: Modules are built to withstand the rigours of transportation. They must be lifted by a crane and travel on highways. This requires a resilient structure, often stronger than some site-built equivalents. Bolting them together creates a very solid home.
- Sustainability: The factory setting allows for better waste management and recycling of materials. Precise cutting reduces scrap. Tighter construction improves energy efficiency, lowering heating and cooling costs. Some factories also use sustainable materials.
-
Building Examples
Modular design isn’t limited to simple boxes. It can achieve remarkable results:
-
-
- Modern Masterpieces: Architects use modules to create stunning, contemporary homes with clean lines, large windows, and open floor plans. Modules can be stacked creatively for multi-story designs.
-
- Charming Cottages: Compact and efficient, modular designs excel at creating cosy, well-designed smaller homes or vacation cabins.
-
- Expansive Family Homes: Large single-storey homes, colonials, and compact pitched-roof homes are commonly built modularly. Modules are joined side-by-side and sometimes stacked to create spacious living areas.
-
- Multi-Family Housing: Modular construction is highly efficient for building apartments, town homes, and student housing, offering speed and consistent quality.
-
- Accessory Dwelling Units (ADUs): Modular construction is ideal for backyard cottages or granny flats, providing a fast and less disruptive way to add living space.
- Complex Shapes: Clever design can combine modules at angles or use non-rectangular modules to create unique shapes that don’t look “boxy.”
-
In Conclusion
Modular home design offers a smart alternative to traditional building. It combines the efficiency and quality control of factory construction with the flexibility and permanence of site-built homes.
By designing the house as a set of interconnected modules built indoors, the process achieves significant advantages: faster construction times, predictable costs, high quality, and strong energy performance. Modern techniques ensure modular homes can be beautiful, customized, and built to last, meeting the same standards as any house on the block.
Frequently Asked Questions:
-
-
- Are modular homes cheaper? Often, yes, but not always drastically. Savings come from faster build time (less labour/financing cost), less material waste, and predictable pricing. The value for the quality is excellent.
-
- Do modular homes look different than a regular house? Not necessarily! Modern modular design offers incredible flexibility. They can look identical to any traditional home style, single-storey homes, colonial, cottage style homes, modern, or have a unique contemporary look. The key is the design chosen.
-
- Are modular homes as strong as regular homes? Yes, and often stronger. Modules must endure transportation stresses, requiring robust construction. Once bolted together on a permanent foundation, they form a very solid structure meeting all local building codes.
-
- How long does it take to build a modular home? The factory build might take 4-12 weeks per module (depending on size/complexity). Site prep and foundation work happen concurrently. Assembly on-site typically takes 1-4 weeks. Overall, it’s usually 30-50% faster than site-built.
-
- Can I customize a modular home? Absolutely! While manufacturers offer plans, customization is a major advantage of modern modular. Work with a modular builder/architect to design a home catered for specific needs, within transportation limits.
-
- What are the financing differences? Financing a modular home is very similar to financing a site-built home. You typically get a standard construction loan that converts to a permanent mortgage once the home is complete and certified. Some lenders specialise in modular construction loans.
-
- Do modular homes depreciate? No. Because they are built to local codes and placed on permanent foundations, modular homes appreciate in value over time, just like traditional site-built homes. This is different from manufactured (mobile) homes.
-
- What about resale value? Resale value is generally comparable to similar site-built homes in the same area. There is typically no distinction on property records or appraisals between a well-built modular home and a site-built home.
- Are there limitations on where I can build? The main limitations relate to transportation access. The route from the factory to the site must accommodate the large trucks and modules. Very narrow roads, low bridges, or steep, winding driveways can pose challenges that need planning. Local zoning rules also apply, just like any build.
-
[/vc_column_text][/vc_column][/vc_row]
-
-
- Building Codes: Modular homes must meet the exact same local and state building codes as traditional site-built homes. They are inspected at the factory and again on-site. Manufactured homes follow the national or regional codes or regulations.
-
- Foundation: Modular homes are placed on a permanent foundation (basement, crawl space, or slab) just like a site-built house. Manufactured homes are often placed on piers or blocks, though they can sometimes be put on a foundation.
-
- Design Flexibility: Modern modular construction offers tremendous design flexibility. While there are practical limits based on transportation, modular homes can look like any traditional house: sleek urban layouts, countryside cottages or multi-storey family homes, even complex modern designs. Manufactured homes often have a recognisable style due to transportation width restrictions.
- Appreciation: Because they meet local codes and are on permanent foundations, modular homes appreciate in value similarly to site-built homes. Manufactured homes typically depreciate, like vehicles.
-
Construction Process of Modular Homes
Understanding how a modular home is built helps explain the design needs. Here’s the typical journey:
-
- Design & Engineering: This is the crucial first step. Architects and engineers work together, often using specialized software. They design the entire house, but broken down into transportable modules.
They determine:
- Design & Engineering: This is the crucial first step. Architects and engineers work together, often using specialized software. They design the entire house, but broken down into transportable modules.
-
-
- Module Size & Shape: How big can each box be to fit on a truck and navigate roads? (Usually max 16 feet wide, 60-70 feet long, but heights vary depending on country and region).
-
- Factory Workflow: How will the module move through the factory assembly line efficiently? What gets installed at each station?
- Approvals: Detailed plans are submitted for local building permits, just like a site-built home.
-
2. Factory Construction:
-
-
- Building the Box: Construction starts on a jig (a precise frame) ensuring perfect dimensions. The floor frame is built first.
-
- Walls Go Up: Exterior and interior walls are framed and stood up on the floor. Sheathing (the outer layer, like plywood) is applied.
-
- Roofing: The roof structure is built and often covered right there in the factory.
-
- Utilities Rough-In: Plumbing pipes and electrical wires are installed inside the walls, floors, and ceilings. HVAC ductwork may also be installed.
-
- Insulation: High-quality insulation is carefully placed in all walls, floors, and ceilings.
-
- Drywall: Interior walls and ceilings get covered with drywall, which is taped, mudded, and sanded smooth.
-
- Interior Finishes: Priming, painting, installing cabinets, countertops, flooring, trim, doors, and even bathroom fixtures often happen in the factory. Appliances might be installed or prepped.
-
- Quality Control: Rigorous inspections happen throughout the process. The finished module is checked against plans.
- Weather Protection: Modules are wrapped tightly for transport to protect against weather and road debris.
-
In many cases, 70–90% of the home is completed before it even leaves the factory.
3. Transportation & Site Prep: While modules are built, the building site is prepared. The foundation (basement, crawl space, or slab) is constructed and inspected. Simultaneously, specialized trucks transport the modules, one or two at a time, to the site. This requires careful route planning.
Proper site preparation ensures that when the modules arrive, everything can be fitted quickly and securely.
4. Crane & Set: A large crane lifts each module off the truck and carefully places it onto the foundation. This is a dramatic and precise operation.
5. Assembly & Finishing:
-
-
- Joining Modules: Modules are bolted together structurally. The roof sections are joined.
-
- Sealing Joints: The seams where modules meet (both inside and outside) are meticulously sealed and flashed to make them weathertight and invisible.
-
- Utility Connections: Electricians and plumbers connect the wiring and plumbing between modules and hook up to the main utilities (septic/sewer, water, electricity, gas).
- HVAC Connections: Ductwork sections between modules are connected, and the system is tested. Skilled workers then handle the sealing, joining, and alignment. This stage is fast; some homes are assembled in just a few days.
-
6. Final Finishes and Inspection
Once assembled, the home undergoes finishing touches. This may include flooring, light fittings, cabinet installations, and paint touch-ups. Then, a final inspection is done to ensure everything meets local building codes. At this point, the home is move-in ready.
Why choose modular? The advantages are compelling:
-
-
- Speed: This is a huge factor. Because factory work happens simultaneously with site prep, and bad weather doesn’t delay indoor construction, the overall build time is significantly faster; often 30-50% quicker than traditional building, that is assuming there are no delays in traditional building due to due to weather, labour shortages, or material supply issues. You move in sooner.
-
- Cost Efficiency: While the base price per square foot might be similar, modular building offers real savings. Faster construction means lower labour costs and financing costs. Less material waste in the controlled factory environment saves money. Predictable pricing is also easier to achieve.
-
- Quality Control: Building in a controlled factory environment is key. Materials are stored properly and protected from weather damage. Skilled workers follow precise processes with constant supervision. Consistent inspections throughout construction ensure high standards. This often results in a tighter, more energy-efficient building envelope.
-
- Scheduling Certainty: Factory production schedules are precise. Weather delays are mostly eliminated. This leads to much greater predictability for move-in dates.
-
- Design Flexibility: Forget the old stereotypes. Modern modular design is highly flexible. Architects can create custom designs, or you can choose from numerous plans offered by modular manufacturers. Styles range from traditional to ultra-modern.
-
- Strength: Modules are built to withstand the rigours of transportation. They must be lifted by a crane and travel on highways. This requires a resilient structure, often stronger than some site-built equivalents. Bolting them together creates a very solid home.
- Sustainability: The factory setting allows for better waste management and recycling of materials. Precise cutting reduces scrap. Tighter construction improves energy efficiency, lowering heating and cooling costs. Some factories also use sustainable materials.
-
Building Examples
Modular design isn’t limited to simple boxes. It can achieve remarkable results:
-
-
- Modern Masterpieces: Architects use modules to create stunning, contemporary homes with clean lines, large windows, and open floor plans. Modules can be stacked creatively for multi-story designs.
-
- Charming Cottages: Compact and efficient, modular designs excel at creating cosy, well-designed smaller homes or vacation cabins.
-
- Expansive Family Homes: Large single-storey homes, colonials, and compact pitched-roof homes are commonly built modularly. Modules are joined side-by-side and sometimes stacked to create spacious living areas.
-
- Multi-Family Housing: Modular construction is highly efficient for building apartments, town homes, and student housing, offering speed and consistent quality.
-
- Accessory Dwelling Units (ADUs): Modular construction is ideal for backyard cottages or granny flats, providing a fast and less disruptive way to add living space.
- Complex Shapes: Clever design can combine modules at angles or use non-rectangular modules to create unique shapes that don’t look “boxy.”
-
In Conclusion
Modular home design offers a smart alternative to traditional building. It combines the efficiency and quality control of factory construction with the flexibility and permanence of site-built homes.
By designing the house as a set of interconnected modules built indoors, the process achieves significant advantages: faster construction times, predictable costs, high quality, and strong energy performance. Modern techniques ensure modular homes can be beautiful, customized, and built to last, meeting the same standards as any house on the block.
Frequently Asked Questions:
-
-
- Are modular homes cheaper? Often, yes, but not always drastically. Savings come from faster build time (less labour/financing cost), less material waste, and predictable pricing. The value for the quality is excellent.
-
- Do modular homes look different than a regular house? Not necessarily! Modern modular design offers incredible flexibility. They can look identical to any traditional home style, single-storey homes, colonial, cottage style homes, modern, or have a unique contemporary look. The key is the design chosen.
-
- Are modular homes as strong as regular homes? Yes, and often stronger. Modules must endure transportation stresses, requiring robust construction. Once bolted together on a permanent foundation, they form a very solid structure meeting all local building codes.
-
- How long does it take to build a modular home? The factory build might take 4-12 weeks per module (depending on size/complexity). Site prep and foundation work happen concurrently. Assembly on-site typically takes 1-4 weeks. Overall, it’s usually 30-50% faster than site-built.
-
- Can I customize a modular home? Absolutely! While manufacturers offer plans, customization is a major advantage of modern modular. Work with a modular builder/architect to design a home catered for specific needs, within transportation limits.
-
- What are the financing differences? Financing a modular home is very similar to financing a site-built home. You typically get a standard construction loan that converts to a permanent mortgage once the home is complete and certified. Some lenders specialise in modular construction loans.
-
- Do modular homes depreciate? No. Because they are built to local codes and placed on permanent foundations, modular homes appreciate in value over time, just like traditional site-built homes. This is different from manufactured (mobile) homes.
-
- What about resale value? Resale value is generally comparable to similar site-built homes in the same area. There is typically no distinction on property records or appraisals between a well-built modular home and a site-built home.
- Are there limitations on where I can build? The main limitations relate to transportation access. The route from the factory to the site must accommodate the large trucks and modules. Very narrow roads, low bridges, or steep, winding driveways can pose challenges that need planning. Local zoning rules also apply, just like any build.
-
[/vc_column_text][/vc_column][/vc_row]
To summarise:
-
-
- All modular homes are prefabricated, but not all prefabricated structures are modular.
-
- Modular homes are delivered in large, mostly complete sections.
- Prefabricated elements can be as small as a window frame or as large as an entire wall. However, the biggest differences between modular and other prefab types, especially manufactured homes, are:
-
-
-
- Building Codes: Modular homes must meet the exact same local and state building codes as traditional site-built homes. They are inspected at the factory and again on-site. Manufactured homes follow the national or regional codes or regulations.
-
- Foundation: Modular homes are placed on a permanent foundation (basement, crawl space, or slab) just like a site-built house. Manufactured homes are often placed on piers or blocks, though they can sometimes be put on a foundation.
-
- Design Flexibility: Modern modular construction offers tremendous design flexibility. While there are practical limits based on transportation, modular homes can look like any traditional house: sleek urban layouts, countryside cottages or multi-storey family homes, even complex modern designs. Manufactured homes often have a recognisable style due to transportation width restrictions.
- Appreciation: Because they meet local codes and are on permanent foundations, modular homes appreciate in value similarly to site-built homes. Manufactured homes typically depreciate, like vehicles.
-
Construction Process of Modular Homes
Understanding how a modular home is built helps explain the design needs. Here’s the typical journey:
-
- Design & Engineering: This is the crucial first step. Architects and engineers work together, often using specialized software. They design the entire house, but broken down into transportable modules.
They determine:
- Design & Engineering: This is the crucial first step. Architects and engineers work together, often using specialized software. They design the entire house, but broken down into transportable modules.
-
-
- Module Size & Shape: How big can each box be to fit on a truck and navigate roads? (Usually max 16 feet wide, 60-70 feet long, but heights vary depending on country and region).
-
- Factory Workflow: How will the module move through the factory assembly line efficiently? What gets installed at each station?
- Approvals: Detailed plans are submitted for local building permits, just like a site-built home.
-
2. Factory Construction:
-
-
- Building the Box: Construction starts on a jig (a precise frame) ensuring perfect dimensions. The floor frame is built first.
-
- Walls Go Up: Exterior and interior walls are framed and stood up on the floor. Sheathing (the outer layer, like plywood) is applied.
-
- Roofing: The roof structure is built and often covered right there in the factory.
-
- Utilities Rough-In: Plumbing pipes and electrical wires are installed inside the walls, floors, and ceilings. HVAC ductwork may also be installed.
-
- Insulation: High-quality insulation is carefully placed in all walls, floors, and ceilings.
-
- Drywall: Interior walls and ceilings get covered with drywall, which is taped, mudded, and sanded smooth.
-
- Interior Finishes: Priming, painting, installing cabinets, countertops, flooring, trim, doors, and even bathroom fixtures often happen in the factory. Appliances might be installed or prepped.
-
- Quality Control: Rigorous inspections happen throughout the process. The finished module is checked against plans.
- Weather Protection: Modules are wrapped tightly for transport to protect against weather and road debris.
-
In many cases, 70–90% of the home is completed before it even leaves the factory.
3. Transportation & Site Prep: While modules are built, the building site is prepared. The foundation (basement, crawl space, or slab) is constructed and inspected. Simultaneously, specialized trucks transport the modules, one or two at a time, to the site. This requires careful route planning.
Proper site preparation ensures that when the modules arrive, everything can be fitted quickly and securely.
4. Crane & Set: A large crane lifts each module off the truck and carefully places it onto the foundation. This is a dramatic and precise operation.
5. Assembly & Finishing:
-
-
- Joining Modules: Modules are bolted together structurally. The roof sections are joined.
-
- Sealing Joints: The seams where modules meet (both inside and outside) are meticulously sealed and flashed to make them weathertight and invisible.
-
- Utility Connections: Electricians and plumbers connect the wiring and plumbing between modules and hook up to the main utilities (septic/sewer, water, electricity, gas).
- HVAC Connections: Ductwork sections between modules are connected, and the system is tested. Skilled workers then handle the sealing, joining, and alignment. This stage is fast; some homes are assembled in just a few days.
-
6. Final Finishes and Inspection
Once assembled, the home undergoes finishing touches. This may include flooring, light fittings, cabinet installations, and paint touch-ups. Then, a final inspection is done to ensure everything meets local building codes. At this point, the home is move-in ready.
Why choose modular? The advantages are compelling:
-
-
- Speed: This is a huge factor. Because factory work happens simultaneously with site prep, and bad weather doesn’t delay indoor construction, the overall build time is significantly faster; often 30-50% quicker than traditional building, that is assuming there are no delays in traditional building due to due to weather, labour shortages, or material supply issues. You move in sooner.
-
- Cost Efficiency: While the base price per square foot might be similar, modular building offers real savings. Faster construction means lower labour costs and financing costs. Less material waste in the controlled factory environment saves money. Predictable pricing is also easier to achieve.
-
- Quality Control: Building in a controlled factory environment is key. Materials are stored properly and protected from weather damage. Skilled workers follow precise processes with constant supervision. Consistent inspections throughout construction ensure high standards. This often results in a tighter, more energy-efficient building envelope.
-
- Scheduling Certainty: Factory production schedules are precise. Weather delays are mostly eliminated. This leads to much greater predictability for move-in dates.
-
- Design Flexibility: Forget the old stereotypes. Modern modular design is highly flexible. Architects can create custom designs, or you can choose from numerous plans offered by modular manufacturers. Styles range from traditional to ultra-modern.
-
- Strength: Modules are built to withstand the rigours of transportation. They must be lifted by a crane and travel on highways. This requires a resilient structure, often stronger than some site-built equivalents. Bolting them together creates a very solid home.
- Sustainability: The factory setting allows for better waste management and recycling of materials. Precise cutting reduces scrap. Tighter construction improves energy efficiency, lowering heating and cooling costs. Some factories also use sustainable materials.
-
Building Examples
Modular design isn’t limited to simple boxes. It can achieve remarkable results:
-
-
- Modern Masterpieces: Architects use modules to create stunning, contemporary homes with clean lines, large windows, and open floor plans. Modules can be stacked creatively for multi-story designs.
-
- Charming Cottages: Compact and efficient, modular designs excel at creating cosy, well-designed smaller homes or vacation cabins.
-
- Expansive Family Homes: Large single-storey homes, colonials, and compact pitched-roof homes are commonly built modularly. Modules are joined side-by-side and sometimes stacked to create spacious living areas.
-
- Multi-Family Housing: Modular construction is highly efficient for building apartments, town homes, and student housing, offering speed and consistent quality.
-
- Accessory Dwelling Units (ADUs): Modular construction is ideal for backyard cottages or granny flats, providing a fast and less disruptive way to add living space.
- Complex Shapes: Clever design can combine modules at angles or use non-rectangular modules to create unique shapes that don’t look “boxy.”
-
In Conclusion
Modular home design offers a smart alternative to traditional building. It combines the efficiency and quality control of factory construction with the flexibility and permanence of site-built homes.
By designing the house as a set of interconnected modules built indoors, the process achieves significant advantages: faster construction times, predictable costs, high quality, and strong energy performance. Modern techniques ensure modular homes can be beautiful, customized, and built to last, meeting the same standards as any house on the block.
Frequently Asked Questions:
-
-
- Are modular homes cheaper? Often, yes, but not always drastically. Savings come from faster build time (less labour/financing cost), less material waste, and predictable pricing. The value for the quality is excellent.
-
- Do modular homes look different than a regular house? Not necessarily! Modern modular design offers incredible flexibility. They can look identical to any traditional home style, single-storey homes, colonial, cottage style homes, modern, or have a unique contemporary look. The key is the design chosen.
-
- Are modular homes as strong as regular homes? Yes, and often stronger. Modules must endure transportation stresses, requiring robust construction. Once bolted together on a permanent foundation, they form a very solid structure meeting all local building codes.
-
- How long does it take to build a modular home? The factory build might take 4-12 weeks per module (depending on size/complexity). Site prep and foundation work happen concurrently. Assembly on-site typically takes 1-4 weeks. Overall, it’s usually 30-50% faster than site-built.
-
- Can I customize a modular home? Absolutely! While manufacturers offer plans, customization is a major advantage of modern modular. Work with a modular builder/architect to design a home catered for specific needs, within transportation limits.
-
- What are the financing differences? Financing a modular home is very similar to financing a site-built home. You typically get a standard construction loan that converts to a permanent mortgage once the home is complete and certified. Some lenders specialise in modular construction loans.
-
- Do modular homes depreciate? No. Because they are built to local codes and placed on permanent foundations, modular homes appreciate in value over time, just like traditional site-built homes. This is different from manufactured (mobile) homes.
-
- What about resale value? Resale value is generally comparable to similar site-built homes in the same area. There is typically no distinction on property records or appraisals between a well-built modular home and a site-built home.
- Are there limitations on where I can build? The main limitations relate to transportation access. The route from the factory to the site must accommodate the large trucks and modules. Very narrow roads, low bridges, or steep, winding driveways can pose challenges that need planning. Local zoning rules also apply, just like any build.
-
[/vc_column_text][/vc_column][/vc_row]
Other types of prefabricated structures include:
-
-
- Panelised homes: Walls and floors are built in panels, then assembled on-site.
-
- Pre-cut homes: Materials are pre-measured and cut in a factory but assembled entirely on-site.
- Container homes: Shipping containers are repurposed into housing units.
-
Compared to these, modular homes usually offer better structural strength, faster assembly, and more flexibility in design.
To summarise:
-
-
- All modular homes are prefabricated, but not all prefabricated structures are modular.
-
- Modular homes are delivered in large, mostly complete sections.
- Prefabricated elements can be as small as a window frame or as large as an entire wall. However, the biggest differences between modular and other prefab types, especially manufactured homes, are:
-
-
-
- Building Codes: Modular homes must meet the exact same local and state building codes as traditional site-built homes. They are inspected at the factory and again on-site. Manufactured homes follow the national or regional codes or regulations.
-
- Foundation: Modular homes are placed on a permanent foundation (basement, crawl space, or slab) just like a site-built house. Manufactured homes are often placed on piers or blocks, though they can sometimes be put on a foundation.
-
- Design Flexibility: Modern modular construction offers tremendous design flexibility. While there are practical limits based on transportation, modular homes can look like any traditional house: sleek urban layouts, countryside cottages or multi-storey family homes, even complex modern designs. Manufactured homes often have a recognisable style due to transportation width restrictions.
- Appreciation: Because they meet local codes and are on permanent foundations, modular homes appreciate in value similarly to site-built homes. Manufactured homes typically depreciate, like vehicles.
-
Construction Process of Modular Homes
Understanding how a modular home is built helps explain the design needs. Here’s the typical journey:
-
- Design & Engineering: This is the crucial first step. Architects and engineers work together, often using specialized software. They design the entire house, but broken down into transportable modules.
They determine:
- Design & Engineering: This is the crucial first step. Architects and engineers work together, often using specialized software. They design the entire house, but broken down into transportable modules.
-
-
- Module Size & Shape: How big can each box be to fit on a truck and navigate roads? (Usually max 16 feet wide, 60-70 feet long, but heights vary depending on country and region).
-
- Factory Workflow: How will the module move through the factory assembly line efficiently? What gets installed at each station?
- Approvals: Detailed plans are submitted for local building permits, just like a site-built home.
-
2. Factory Construction:
-
-
- Building the Box: Construction starts on a jig (a precise frame) ensuring perfect dimensions. The floor frame is built first.
-
- Walls Go Up: Exterior and interior walls are framed and stood up on the floor. Sheathing (the outer layer, like plywood) is applied.
-
- Roofing: The roof structure is built and often covered right there in the factory.
-
- Utilities Rough-In: Plumbing pipes and electrical wires are installed inside the walls, floors, and ceilings. HVAC ductwork may also be installed.
-
- Insulation: High-quality insulation is carefully placed in all walls, floors, and ceilings.
-
- Drywall: Interior walls and ceilings get covered with drywall, which is taped, mudded, and sanded smooth.
-
- Interior Finishes: Priming, painting, installing cabinets, countertops, flooring, trim, doors, and even bathroom fixtures often happen in the factory. Appliances might be installed or prepped.
-
- Quality Control: Rigorous inspections happen throughout the process. The finished module is checked against plans.
- Weather Protection: Modules are wrapped tightly for transport to protect against weather and road debris.
-
In many cases, 70–90% of the home is completed before it even leaves the factory.
3. Transportation & Site Prep: While modules are built, the building site is prepared. The foundation (basement, crawl space, or slab) is constructed and inspected. Simultaneously, specialized trucks transport the modules, one or two at a time, to the site. This requires careful route planning.
Proper site preparation ensures that when the modules arrive, everything can be fitted quickly and securely.
4. Crane & Set: A large crane lifts each module off the truck and carefully places it onto the foundation. This is a dramatic and precise operation.
5. Assembly & Finishing:
-
-
- Joining Modules: Modules are bolted together structurally. The roof sections are joined.
-
- Sealing Joints: The seams where modules meet (both inside and outside) are meticulously sealed and flashed to make them weathertight and invisible.
-
- Utility Connections: Electricians and plumbers connect the wiring and plumbing between modules and hook up to the main utilities (septic/sewer, water, electricity, gas).
- HVAC Connections: Ductwork sections between modules are connected, and the system is tested. Skilled workers then handle the sealing, joining, and alignment. This stage is fast; some homes are assembled in just a few days.
-
6. Final Finishes and Inspection
Once assembled, the home undergoes finishing touches. This may include flooring, light fittings, cabinet installations, and paint touch-ups. Then, a final inspection is done to ensure everything meets local building codes. At this point, the home is move-in ready.
Why choose modular? The advantages are compelling:
-
-
- Speed: This is a huge factor. Because factory work happens simultaneously with site prep, and bad weather doesn’t delay indoor construction, the overall build time is significantly faster; often 30-50% quicker than traditional building, that is assuming there are no delays in traditional building due to due to weather, labour shortages, or material supply issues. You move in sooner.
-
- Cost Efficiency: While the base price per square foot might be similar, modular building offers real savings. Faster construction means lower labour costs and financing costs. Less material waste in the controlled factory environment saves money. Predictable pricing is also easier to achieve.
-
- Quality Control: Building in a controlled factory environment is key. Materials are stored properly and protected from weather damage. Skilled workers follow precise processes with constant supervision. Consistent inspections throughout construction ensure high standards. This often results in a tighter, more energy-efficient building envelope.
-
- Scheduling Certainty: Factory production schedules are precise. Weather delays are mostly eliminated. This leads to much greater predictability for move-in dates.
-
- Design Flexibility: Forget the old stereotypes. Modern modular design is highly flexible. Architects can create custom designs, or you can choose from numerous plans offered by modular manufacturers. Styles range from traditional to ultra-modern.
-
- Strength: Modules are built to withstand the rigours of transportation. They must be lifted by a crane and travel on highways. This requires a resilient structure, often stronger than some site-built equivalents. Bolting them together creates a very solid home.
- Sustainability: The factory setting allows for better waste management and recycling of materials. Precise cutting reduces scrap. Tighter construction improves energy efficiency, lowering heating and cooling costs. Some factories also use sustainable materials.
-
Building Examples
Modular design isn’t limited to simple boxes. It can achieve remarkable results:
-
-
- Modern Masterpieces: Architects use modules to create stunning, contemporary homes with clean lines, large windows, and open floor plans. Modules can be stacked creatively for multi-story designs.
-
- Charming Cottages: Compact and efficient, modular designs excel at creating cosy, well-designed smaller homes or vacation cabins.
-
- Expansive Family Homes: Large single-storey homes, colonials, and compact pitched-roof homes are commonly built modularly. Modules are joined side-by-side and sometimes stacked to create spacious living areas.
-
- Multi-Family Housing: Modular construction is highly efficient for building apartments, town homes, and student housing, offering speed and consistent quality.
-
- Accessory Dwelling Units (ADUs): Modular construction is ideal for backyard cottages or granny flats, providing a fast and less disruptive way to add living space.
- Complex Shapes: Clever design can combine modules at angles or use non-rectangular modules to create unique shapes that don’t look “boxy.”
-
In Conclusion
Modular home design offers a smart alternative to traditional building. It combines the efficiency and quality control of factory construction with the flexibility and permanence of site-built homes.
By designing the house as a set of interconnected modules built indoors, the process achieves significant advantages: faster construction times, predictable costs, high quality, and strong energy performance. Modern techniques ensure modular homes can be beautiful, customized, and built to last, meeting the same standards as any house on the block.
Frequently Asked Questions:
-
-
- Are modular homes cheaper? Often, yes, but not always drastically. Savings come from faster build time (less labour/financing cost), less material waste, and predictable pricing. The value for the quality is excellent.
-
- Do modular homes look different than a regular house? Not necessarily! Modern modular design offers incredible flexibility. They can look identical to any traditional home style, single-storey homes, colonial, cottage style homes, modern, or have a unique contemporary look. The key is the design chosen.
-
- Are modular homes as strong as regular homes? Yes, and often stronger. Modules must endure transportation stresses, requiring robust construction. Once bolted together on a permanent foundation, they form a very solid structure meeting all local building codes.
-
- How long does it take to build a modular home? The factory build might take 4-12 weeks per module (depending on size/complexity). Site prep and foundation work happen concurrently. Assembly on-site typically takes 1-4 weeks. Overall, it’s usually 30-50% faster than site-built.
-
- Can I customize a modular home? Absolutely! While manufacturers offer plans, customization is a major advantage of modern modular. Work with a modular builder/architect to design a home catered for specific needs, within transportation limits.
-
- What are the financing differences? Financing a modular home is very similar to financing a site-built home. You typically get a standard construction loan that converts to a permanent mortgage once the home is complete and certified. Some lenders specialise in modular construction loans.
-
- Do modular homes depreciate? No. Because they are built to local codes and placed on permanent foundations, modular homes appreciate in value over time, just like traditional site-built homes. This is different from manufactured (mobile) homes.
-
- What about resale value? Resale value is generally comparable to similar site-built homes in the same area. There is typically no distinction on property records or appraisals between a well-built modular home and a site-built home.
- Are there limitations on where I can build? The main limitations relate to transportation access. The route from the factory to the site must accommodate the large trucks and modules. Very narrow roads, low bridges, or steep, winding driveways can pose challenges that need planning. Local zoning rules also apply, just like any build.
-
[/vc_column_text][/vc_column][/vc_row]
Modular Homes v/s Prefabricated StructuresThe words “modular” and “prefab” (short for prefabricated) are often used together, sometimes even interchangeably. This can be confusing. It’s helpful to understand that prefab is a broad category. It simply means any part of a building is made before it arrives at the construction site.
Prefab or prefabricated refers to any part of a building that is made off-site. It can include wall panels, roof trusses, or even smaller sections like window frames. Prefab is a broad term. Modular homes fall under this category, but they are a specific kind of prefab construction.
Modular refers to building entire sections of a house; full rooms or parts of rooms in a factory setting. These modules are often built complete with wiring, plumbing, insulation, and flooring. They are transported to the building site and joined together like large building blocks.
Other types of prefabricated structures include:
-
-
- Panelised homes: Walls and floors are built in panels, then assembled on-site.
-
- Pre-cut homes: Materials are pre-measured and cut in a factory but assembled entirely on-site.
- Container homes: Shipping containers are repurposed into housing units.
-
Compared to these, modular homes usually offer better structural strength, faster assembly, and more flexibility in design.
To summarise:
-
-
- All modular homes are prefabricated, but not all prefabricated structures are modular.
-
- Modular homes are delivered in large, mostly complete sections.
- Prefabricated elements can be as small as a window frame or as large as an entire wall. However, the biggest differences between modular and other prefab types, especially manufactured homes, are:
-
-
-
- Building Codes: Modular homes must meet the exact same local and state building codes as traditional site-built homes. They are inspected at the factory and again on-site. Manufactured homes follow the national or regional codes or regulations.
-
- Foundation: Modular homes are placed on a permanent foundation (basement, crawl space, or slab) just like a site-built house. Manufactured homes are often placed on piers or blocks, though they can sometimes be put on a foundation.
-
- Design Flexibility: Modern modular construction offers tremendous design flexibility. While there are practical limits based on transportation, modular homes can look like any traditional house: sleek urban layouts, countryside cottages or multi-storey family homes, even complex modern designs. Manufactured homes often have a recognisable style due to transportation width restrictions.
- Appreciation: Because they meet local codes and are on permanent foundations, modular homes appreciate in value similarly to site-built homes. Manufactured homes typically depreciate, like vehicles.
-
Construction Process of Modular Homes
Understanding how a modular home is built helps explain the design needs. Here’s the typical journey:
-
- Design & Engineering: This is the crucial first step. Architects and engineers work together, often using specialized software. They design the entire house, but broken down into transportable modules.
They determine:
- Design & Engineering: This is the crucial first step. Architects and engineers work together, often using specialized software. They design the entire house, but broken down into transportable modules.
-
-
- Module Size & Shape: How big can each box be to fit on a truck and navigate roads? (Usually max 16 feet wide, 60-70 feet long, but heights vary depending on country and region).
-
- Factory Workflow: How will the module move through the factory assembly line efficiently? What gets installed at each station?
- Approvals: Detailed plans are submitted for local building permits, just like a site-built home.
-
2. Factory Construction:
-
-
- Building the Box: Construction starts on a jig (a precise frame) ensuring perfect dimensions. The floor frame is built first.
-
- Walls Go Up: Exterior and interior walls are framed and stood up on the floor. Sheathing (the outer layer, like plywood) is applied.
-
- Roofing: The roof structure is built and often covered right there in the factory.
-
- Utilities Rough-In: Plumbing pipes and electrical wires are installed inside the walls, floors, and ceilings. HVAC ductwork may also be installed.
-
- Insulation: High-quality insulation is carefully placed in all walls, floors, and ceilings.
-
- Drywall: Interior walls and ceilings get covered with drywall, which is taped, mudded, and sanded smooth.
-
- Interior Finishes: Priming, painting, installing cabinets, countertops, flooring, trim, doors, and even bathroom fixtures often happen in the factory. Appliances might be installed or prepped.
-
- Quality Control: Rigorous inspections happen throughout the process. The finished module is checked against plans.
- Weather Protection: Modules are wrapped tightly for transport to protect against weather and road debris.
-
In many cases, 70–90% of the home is completed before it even leaves the factory.
3. Transportation & Site Prep: While modules are built, the building site is prepared. The foundation (basement, crawl space, or slab) is constructed and inspected. Simultaneously, specialized trucks transport the modules, one or two at a time, to the site. This requires careful route planning.
Proper site preparation ensures that when the modules arrive, everything can be fitted quickly and securely.
4. Crane & Set: A large crane lifts each module off the truck and carefully places it onto the foundation. This is a dramatic and precise operation.
5. Assembly & Finishing:
-
-
- Joining Modules: Modules are bolted together structurally. The roof sections are joined.
-
- Sealing Joints: The seams where modules meet (both inside and outside) are meticulously sealed and flashed to make them weathertight and invisible.
-
- Utility Connections: Electricians and plumbers connect the wiring and plumbing between modules and hook up to the main utilities (septic/sewer, water, electricity, gas).
- HVAC Connections: Ductwork sections between modules are connected, and the system is tested. Skilled workers then handle the sealing, joining, and alignment. This stage is fast; some homes are assembled in just a few days.
-
6. Final Finishes and Inspection
Once assembled, the home undergoes finishing touches. This may include flooring, light fittings, cabinet installations, and paint touch-ups. Then, a final inspection is done to ensure everything meets local building codes. At this point, the home is move-in ready.
Why choose modular? The advantages are compelling:
-
-
- Speed: This is a huge factor. Because factory work happens simultaneously with site prep, and bad weather doesn’t delay indoor construction, the overall build time is significantly faster; often 30-50% quicker than traditional building, that is assuming there are no delays in traditional building due to due to weather, labour shortages, or material supply issues. You move in sooner.
-
- Cost Efficiency: While the base price per square foot might be similar, modular building offers real savings. Faster construction means lower labour costs and financing costs. Less material waste in the controlled factory environment saves money. Predictable pricing is also easier to achieve.
-
- Quality Control: Building in a controlled factory environment is key. Materials are stored properly and protected from weather damage. Skilled workers follow precise processes with constant supervision. Consistent inspections throughout construction ensure high standards. This often results in a tighter, more energy-efficient building envelope.
-
- Scheduling Certainty: Factory production schedules are precise. Weather delays are mostly eliminated. This leads to much greater predictability for move-in dates.
-
- Design Flexibility: Forget the old stereotypes. Modern modular design is highly flexible. Architects can create custom designs, or you can choose from numerous plans offered by modular manufacturers. Styles range from traditional to ultra-modern.
-
- Strength: Modules are built to withstand the rigours of transportation. They must be lifted by a crane and travel on highways. This requires a resilient structure, often stronger than some site-built equivalents. Bolting them together creates a very solid home.
- Sustainability: The factory setting allows for better waste management and recycling of materials. Precise cutting reduces scrap. Tighter construction improves energy efficiency, lowering heating and cooling costs. Some factories also use sustainable materials.
-
Building Examples
Modular design isn’t limited to simple boxes. It can achieve remarkable results:
-
-
- Modern Masterpieces: Architects use modules to create stunning, contemporary homes with clean lines, large windows, and open floor plans. Modules can be stacked creatively for multi-story designs.
-
- Charming Cottages: Compact and efficient, modular designs excel at creating cosy, well-designed smaller homes or vacation cabins.
-
- Expansive Family Homes: Large single-storey homes, colonials, and compact pitched-roof homes are commonly built modularly. Modules are joined side-by-side and sometimes stacked to create spacious living areas.
-
- Multi-Family Housing: Modular construction is highly efficient for building apartments, town homes, and student housing, offering speed and consistent quality.
-
- Accessory Dwelling Units (ADUs): Modular construction is ideal for backyard cottages or granny flats, providing a fast and less disruptive way to add living space.
- Complex Shapes: Clever design can combine modules at angles or use non-rectangular modules to create unique shapes that don’t look “boxy.”
-
In Conclusion
Modular home design offers a smart alternative to traditional building. It combines the efficiency and quality control of factory construction with the flexibility and permanence of site-built homes.
By designing the house as a set of interconnected modules built indoors, the process achieves significant advantages: faster construction times, predictable costs, high quality, and strong energy performance. Modern techniques ensure modular homes can be beautiful, customized, and built to last, meeting the same standards as any house on the block.
Frequently Asked Questions:
-
-
- Are modular homes cheaper? Often, yes, but not always drastically. Savings come from faster build time (less labour/financing cost), less material waste, and predictable pricing. The value for the quality is excellent.
-
- Do modular homes look different than a regular house? Not necessarily! Modern modular design offers incredible flexibility. They can look identical to any traditional home style, single-storey homes, colonial, cottage style homes, modern, or have a unique contemporary look. The key is the design chosen.
-
- Are modular homes as strong as regular homes? Yes, and often stronger. Modules must endure transportation stresses, requiring robust construction. Once bolted together on a permanent foundation, they form a very solid structure meeting all local building codes.
-
- How long does it take to build a modular home? The factory build might take 4-12 weeks per module (depending on size/complexity). Site prep and foundation work happen concurrently. Assembly on-site typically takes 1-4 weeks. Overall, it’s usually 30-50% faster than site-built.
-
- Can I customize a modular home? Absolutely! While manufacturers offer plans, customization is a major advantage of modern modular. Work with a modular builder/architect to design a home catered for specific needs, within transportation limits.
-
- What are the financing differences? Financing a modular home is very similar to financing a site-built home. You typically get a standard construction loan that converts to a permanent mortgage once the home is complete and certified. Some lenders specialise in modular construction loans.
-
- Do modular homes depreciate? No. Because they are built to local codes and placed on permanent foundations, modular homes appreciate in value over time, just like traditional site-built homes. This is different from manufactured (mobile) homes.
-
- What about resale value? Resale value is generally comparable to similar site-built homes in the same area. There is typically no distinction on property records or appraisals between a well-built modular home and a site-built home.
- Are there limitations on where I can build? The main limitations relate to transportation access. The route from the factory to the site must accommodate the large trucks and modules. Very narrow roads, low bridges, or steep, winding driveways can pose challenges that need planning. Local zoning rules also apply, just like any build.
-
[/vc_column_text][/vc_column][/vc_row]
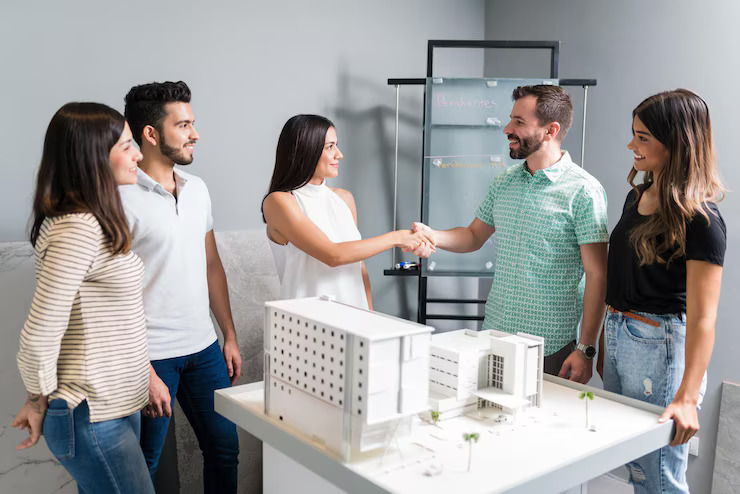
What Are Modular Homes?
A modular home is a house made up of separate sections called modules. These modules are built off-site, usually in a factory. Each module may be a room or a set of rooms. Once complete, the modules are moved to the construction site and placed on a solid foundation.
These are not temporary homes or mobile homes. Modular homes are permanent, just like regular houses built brick by brick on location. They follow the same safety and building codes and often match or even exceed the standards used in conventional construction.
The main idea is to separate the construction into smaller, manageable parts. Instead of building everything at once at the site, the parts are built in a controlled environment and then brought together. This saves time, reduces error, and often lowers costs.
Modular homes can be one-storey or multi-storey. Some are simple and compact. Others are large, with many rooms, porches, and balconies. The outer look can be made to match almost any style: modern, rustic, minimal, or traditional.
From the inside, modular homes are no different. They have kitchens, living rooms, bathrooms, and bedrooms, designed and decorated to the owner’s taste. Once completed, it’s hard to tell that the home wasn’t built on-site from scratch.
Modular Homes v/s Prefabricated Structures
The words “modular” and “prefab” (short for prefabricated) are often used together, sometimes even interchangeably. This can be confusing. It’s helpful to understand that prefab is a broad category. It simply means any part of a building is made before it arrives at the construction site.
Prefab or prefabricated refers to any part of a building that is made off-site. It can include wall panels, roof trusses, or even smaller sections like window frames. Prefab is a broad term. Modular homes fall under this category, but they are a specific kind of prefab construction.
Modular refers to building entire sections of a house; full rooms or parts of rooms in a factory setting. These modules are often built complete with wiring, plumbing, insulation, and flooring. They are transported to the building site and joined together like large building blocks.
Other types of prefabricated structures include:
-
-
- Panelised homes: Walls and floors are built in panels, then assembled on-site.
-
- Pre-cut homes: Materials are pre-measured and cut in a factory but assembled entirely on-site.
- Container homes: Shipping containers are repurposed into housing units.
-
Compared to these, modular homes usually offer better structural strength, faster assembly, and more flexibility in design.
To summarise:
-
-
- All modular homes are prefabricated, but not all prefabricated structures are modular.
-
- Modular homes are delivered in large, mostly complete sections.
- Prefabricated elements can be as small as a window frame or as large as an entire wall. However, the biggest differences between modular and other prefab types, especially manufactured homes, are:
-
-
-
- Building Codes: Modular homes must meet the exact same local and state building codes as traditional site-built homes. They are inspected at the factory and again on-site. Manufactured homes follow the national or regional codes or regulations.
-
- Foundation: Modular homes are placed on a permanent foundation (basement, crawl space, or slab) just like a site-built house. Manufactured homes are often placed on piers or blocks, though they can sometimes be put on a foundation.
-
- Design Flexibility: Modern modular construction offers tremendous design flexibility. While there are practical limits based on transportation, modular homes can look like any traditional house: sleek urban layouts, countryside cottages or multi-storey family homes, even complex modern designs. Manufactured homes often have a recognisable style due to transportation width restrictions.
- Appreciation: Because they meet local codes and are on permanent foundations, modular homes appreciate in value similarly to site-built homes. Manufactured homes typically depreciate, like vehicles.
-
Construction Process of Modular Homes
Understanding how a modular home is built helps explain the design needs. Here’s the typical journey:
-
- Design & Engineering: This is the crucial first step. Architects and engineers work together, often using specialized software. They design the entire house, but broken down into transportable modules.
They determine:
- Design & Engineering: This is the crucial first step. Architects and engineers work together, often using specialized software. They design the entire house, but broken down into transportable modules.
-
-
- Module Size & Shape: How big can each box be to fit on a truck and navigate roads? (Usually max 16 feet wide, 60-70 feet long, but heights vary depending on country and region).
-
- Factory Workflow: How will the module move through the factory assembly line efficiently? What gets installed at each station?
- Approvals: Detailed plans are submitted for local building permits, just like a site-built home.
-
2. Factory Construction:
-
-
- Building the Box: Construction starts on a jig (a precise frame) ensuring perfect dimensions. The floor frame is built first.
-
- Walls Go Up: Exterior and interior walls are framed and stood up on the floor. Sheathing (the outer layer, like plywood) is applied.
-
- Roofing: The roof structure is built and often covered right there in the factory.
-
- Utilities Rough-In: Plumbing pipes and electrical wires are installed inside the walls, floors, and ceilings. HVAC ductwork may also be installed.
-
- Insulation: High-quality insulation is carefully placed in all walls, floors, and ceilings.
-
- Drywall: Interior walls and ceilings get covered with drywall, which is taped, mudded, and sanded smooth.
-
- Interior Finishes: Priming, painting, installing cabinets, countertops, flooring, trim, doors, and even bathroom fixtures often happen in the factory. Appliances might be installed or prepped.
-
- Quality Control: Rigorous inspections happen throughout the process. The finished module is checked against plans.
- Weather Protection: Modules are wrapped tightly for transport to protect against weather and road debris.
-
In many cases, 70–90% of the home is completed before it even leaves the factory.
3. Transportation & Site Prep: While modules are built, the building site is prepared. The foundation (basement, crawl space, or slab) is constructed and inspected. Simultaneously, specialized trucks transport the modules, one or two at a time, to the site. This requires careful route planning.
Proper site preparation ensures that when the modules arrive, everything can be fitted quickly and securely.
4. Crane & Set: A large crane lifts each module off the truck and carefully places it onto the foundation. This is a dramatic and precise operation.
5. Assembly & Finishing:
-
-
- Joining Modules: Modules are bolted together structurally. The roof sections are joined.
-
- Sealing Joints: The seams where modules meet (both inside and outside) are meticulously sealed and flashed to make them weathertight and invisible.
-
- Utility Connections: Electricians and plumbers connect the wiring and plumbing between modules and hook up to the main utilities (septic/sewer, water, electricity, gas).
- HVAC Connections: Ductwork sections between modules are connected, and the system is tested. Skilled workers then handle the sealing, joining, and alignment. This stage is fast; some homes are assembled in just a few days.
-
6. Final Finishes and Inspection
Once assembled, the home undergoes finishing touches. This may include flooring, light fittings, cabinet installations, and paint touch-ups. Then, a final inspection is done to ensure everything meets local building codes. At this point, the home is move-in ready.
Why choose modular? The advantages are compelling:
-
-
- Speed: This is a huge factor. Because factory work happens simultaneously with site prep, and bad weather doesn’t delay indoor construction, the overall build time is significantly faster; often 30-50% quicker than traditional building, that is assuming there are no delays in traditional building due to due to weather, labour shortages, or material supply issues. You move in sooner.
-
- Cost Efficiency: While the base price per square foot might be similar, modular building offers real savings. Faster construction means lower labour costs and financing costs. Less material waste in the controlled factory environment saves money. Predictable pricing is also easier to achieve.
-
- Quality Control: Building in a controlled factory environment is key. Materials are stored properly and protected from weather damage. Skilled workers follow precise processes with constant supervision. Consistent inspections throughout construction ensure high standards. This often results in a tighter, more energy-efficient building envelope.
-
- Scheduling Certainty: Factory production schedules are precise. Weather delays are mostly eliminated. This leads to much greater predictability for move-in dates.
-
- Design Flexibility: Forget the old stereotypes. Modern modular design is highly flexible. Architects can create custom designs, or you can choose from numerous plans offered by modular manufacturers. Styles range from traditional to ultra-modern.
-
- Strength: Modules are built to withstand the rigours of transportation. They must be lifted by a crane and travel on highways. This requires a resilient structure, often stronger than some site-built equivalents. Bolting them together creates a very solid home.
- Sustainability: The factory setting allows for better waste management and recycling of materials. Precise cutting reduces scrap. Tighter construction improves energy efficiency, lowering heating and cooling costs. Some factories also use sustainable materials.
-
Building Examples
Modular design isn’t limited to simple boxes. It can achieve remarkable results:
-
-
- Modern Masterpieces: Architects use modules to create stunning, contemporary homes with clean lines, large windows, and open floor plans. Modules can be stacked creatively for multi-story designs.
-
- Charming Cottages: Compact and efficient, modular designs excel at creating cosy, well-designed smaller homes or vacation cabins.
-
- Expansive Family Homes: Large single-storey homes, colonials, and compact pitched-roof homes are commonly built modularly. Modules are joined side-by-side and sometimes stacked to create spacious living areas.
-
- Multi-Family Housing: Modular construction is highly efficient for building apartments, town homes, and student housing, offering speed and consistent quality.
-
- Accessory Dwelling Units (ADUs): Modular construction is ideal for backyard cottages or granny flats, providing a fast and less disruptive way to add living space.
- Complex Shapes: Clever design can combine modules at angles or use non-rectangular modules to create unique shapes that don’t look “boxy.”
-
In Conclusion
Modular home design offers a smart alternative to traditional building. It combines the efficiency and quality control of factory construction with the flexibility and permanence of site-built homes.
By designing the house as a set of interconnected modules built indoors, the process achieves significant advantages: faster construction times, predictable costs, high quality, and strong energy performance. Modern techniques ensure modular homes can be beautiful, customized, and built to last, meeting the same standards as any house on the block.
Frequently Asked Questions:
-
-
- Are modular homes cheaper? Often, yes, but not always drastically. Savings come from faster build time (less labour/financing cost), less material waste, and predictable pricing. The value for the quality is excellent.
-
- Do modular homes look different than a regular house? Not necessarily! Modern modular design offers incredible flexibility. They can look identical to any traditional home style, single-storey homes, colonial, cottage style homes, modern, or have a unique contemporary look. The key is the design chosen.
-
- Are modular homes as strong as regular homes? Yes, and often stronger. Modules must endure transportation stresses, requiring robust construction. Once bolted together on a permanent foundation, they form a very solid structure meeting all local building codes.
-
- How long does it take to build a modular home? The factory build might take 4-12 weeks per module (depending on size/complexity). Site prep and foundation work happen concurrently. Assembly on-site typically takes 1-4 weeks. Overall, it’s usually 30-50% faster than site-built.
-
- Can I customize a modular home? Absolutely! While manufacturers offer plans, customization is a major advantage of modern modular. Work with a modular builder/architect to design a home catered for specific needs, within transportation limits.
-
- What are the financing differences? Financing a modular home is very similar to financing a site-built home. You typically get a standard construction loan that converts to a permanent mortgage once the home is complete and certified. Some lenders specialise in modular construction loans.
-
- Do modular homes depreciate? No. Because they are built to local codes and placed on permanent foundations, modular homes appreciate in value over time, just like traditional site-built homes. This is different from manufactured (mobile) homes.
-
- What about resale value? Resale value is generally comparable to similar site-built homes in the same area. There is typically no distinction on property records or appraisals between a well-built modular home and a site-built home.
- Are there limitations on where I can build? The main limitations relate to transportation access. The route from the factory to the site must accommodate the large trucks and modules. Very narrow roads, low bridges, or steep, winding driveways can pose challenges that need planning. Local zoning rules also apply, just like any build.
-
[/vc_column_text][/vc_column][/vc_row]
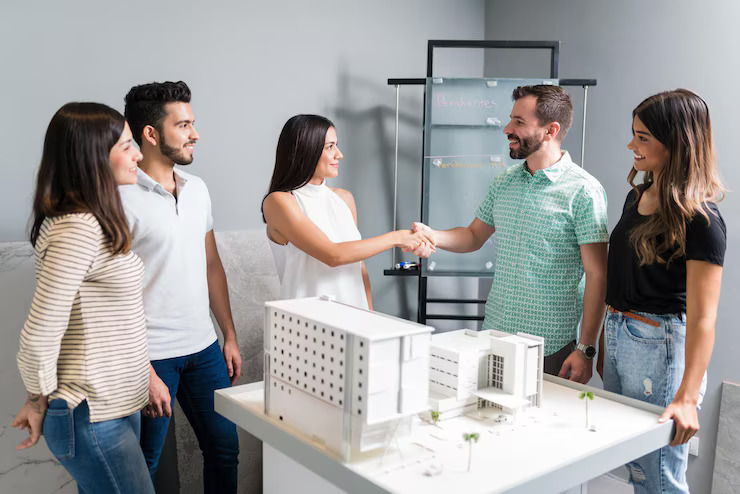
What Are Modular Homes?
A modular home is a house made up of separate sections called modules. These modules are built off-site, usually in a factory. Each module may be a room or a set of rooms. Once complete, the modules are moved to the construction site and placed on a solid foundation.
These are not temporary homes or mobile homes. Modular homes are permanent, just like regular houses built brick by brick on location. They follow the same safety and building codes and often match or even exceed the standards used in conventional construction.
The main idea is to separate the construction into smaller, manageable parts. Instead of building everything at once at the site, the parts are built in a controlled environment and then brought together. This saves time, reduces error, and often lowers costs.
Modular homes can be one-storey or multi-storey. Some are simple and compact. Others are large, with many rooms, porches, and balconies. The outer look can be made to match almost any style: modern, rustic, minimal, or traditional.
From the inside, modular homes are no different. They have kitchens, living rooms, bathrooms, and bedrooms, designed and decorated to the owner’s taste. Once completed, it’s hard to tell that the home wasn’t built on-site from scratch.
Modular Homes v/s Prefabricated Structures
The words “modular” and “prefab” (short for prefabricated) are often used together, sometimes even interchangeably. This can be confusing. It’s helpful to understand that prefab is a broad category. It simply means any part of a building is made before it arrives at the construction site.
Prefab or prefabricated refers to any part of a building that is made off-site. It can include wall panels, roof trusses, or even smaller sections like window frames. Prefab is a broad term. Modular homes fall under this category, but they are a specific kind of prefab construction.
Modular refers to building entire sections of a house; full rooms or parts of rooms in a factory setting. These modules are often built complete with wiring, plumbing, insulation, and flooring. They are transported to the building site and joined together like large building blocks.
Other types of prefabricated structures include:
-
-
- Panelised homes: Walls and floors are built in panels, then assembled on-site.
-
- Pre-cut homes: Materials are pre-measured and cut in a factory but assembled entirely on-site.
- Container homes: Shipping containers are repurposed into housing units.
-
Compared to these, modular homes usually offer better structural strength, faster assembly, and more flexibility in design.
To summarise:
-
-
- All modular homes are prefabricated, but not all prefabricated structures are modular.
-
- Modular homes are delivered in large, mostly complete sections.
- Prefabricated elements can be as small as a window frame or as large as an entire wall. However, the biggest differences between modular and other prefab types, especially manufactured homes, are:
-
-
-
- Building Codes: Modular homes must meet the exact same local and state building codes as traditional site-built homes. They are inspected at the factory and again on-site. Manufactured homes follow the national or regional codes or regulations.
-
- Foundation: Modular homes are placed on a permanent foundation (basement, crawl space, or slab) just like a site-built house. Manufactured homes are often placed on piers or blocks, though they can sometimes be put on a foundation.
-
- Design Flexibility: Modern modular construction offers tremendous design flexibility. While there are practical limits based on transportation, modular homes can look like any traditional house: sleek urban layouts, countryside cottages or multi-storey family homes, even complex modern designs. Manufactured homes often have a recognisable style due to transportation width restrictions.
- Appreciation: Because they meet local codes and are on permanent foundations, modular homes appreciate in value similarly to site-built homes. Manufactured homes typically depreciate, like vehicles.
-
Construction Process of Modular Homes
Understanding how a modular home is built helps explain the design needs. Here’s the typical journey:
-
- Design & Engineering: This is the crucial first step. Architects and engineers work together, often using specialized software. They design the entire house, but broken down into transportable modules.
They determine:
- Design & Engineering: This is the crucial first step. Architects and engineers work together, often using specialized software. They design the entire house, but broken down into transportable modules.
-
-
- Module Size & Shape: How big can each box be to fit on a truck and navigate roads? (Usually max 16 feet wide, 60-70 feet long, but heights vary depending on country and region).
-
- Factory Workflow: How will the module move through the factory assembly line efficiently? What gets installed at each station?
- Approvals: Detailed plans are submitted for local building permits, just like a site-built home.
-
2. Factory Construction:
-
-
- Building the Box: Construction starts on a jig (a precise frame) ensuring perfect dimensions. The floor frame is built first.
-
- Walls Go Up: Exterior and interior walls are framed and stood up on the floor. Sheathing (the outer layer, like plywood) is applied.
-
- Roofing: The roof structure is built and often covered right there in the factory.
-
- Utilities Rough-In: Plumbing pipes and electrical wires are installed inside the walls, floors, and ceilings. HVAC ductwork may also be installed.
-
- Insulation: High-quality insulation is carefully placed in all walls, floors, and ceilings.
-
- Drywall: Interior walls and ceilings get covered with drywall, which is taped, mudded, and sanded smooth.
-
- Interior Finishes: Priming, painting, installing cabinets, countertops, flooring, trim, doors, and even bathroom fixtures often happen in the factory. Appliances might be installed or prepped.
-
- Quality Control: Rigorous inspections happen throughout the process. The finished module is checked against plans.
- Weather Protection: Modules are wrapped tightly for transport to protect against weather and road debris.
-
In many cases, 70–90% of the home is completed before it even leaves the factory.
3. Transportation & Site Prep: While modules are built, the building site is prepared. The foundation (basement, crawl space, or slab) is constructed and inspected. Simultaneously, specialized trucks transport the modules, one or two at a time, to the site. This requires careful route planning.
Proper site preparation ensures that when the modules arrive, everything can be fitted quickly and securely.
4. Crane & Set: A large crane lifts each module off the truck and carefully places it onto the foundation. This is a dramatic and precise operation.
5. Assembly & Finishing:
-
-
- Joining Modules: Modules are bolted together structurally. The roof sections are joined.
-
- Sealing Joints: The seams where modules meet (both inside and outside) are meticulously sealed and flashed to make them weathertight and invisible.
-
- Utility Connections: Electricians and plumbers connect the wiring and plumbing between modules and hook up to the main utilities (septic/sewer, water, electricity, gas).
- HVAC Connections: Ductwork sections between modules are connected, and the system is tested. Skilled workers then handle the sealing, joining, and alignment. This stage is fast; some homes are assembled in just a few days.
-
6. Final Finishes and Inspection
Once assembled, the home undergoes finishing touches. This may include flooring, light fittings, cabinet installations, and paint touch-ups. Then, a final inspection is done to ensure everything meets local building codes. At this point, the home is move-in ready.
Why choose modular? The advantages are compelling:
-
-
- Speed: This is a huge factor. Because factory work happens simultaneously with site prep, and bad weather doesn’t delay indoor construction, the overall build time is significantly faster; often 30-50% quicker than traditional building, that is assuming there are no delays in traditional building due to due to weather, labour shortages, or material supply issues. You move in sooner.
-
- Cost Efficiency: While the base price per square foot might be similar, modular building offers real savings. Faster construction means lower labour costs and financing costs. Less material waste in the controlled factory environment saves money. Predictable pricing is also easier to achieve.
-
- Quality Control: Building in a controlled factory environment is key. Materials are stored properly and protected from weather damage. Skilled workers follow precise processes with constant supervision. Consistent inspections throughout construction ensure high standards. This often results in a tighter, more energy-efficient building envelope.
-
- Scheduling Certainty: Factory production schedules are precise. Weather delays are mostly eliminated. This leads to much greater predictability for move-in dates.
-
- Design Flexibility: Forget the old stereotypes. Modern modular design is highly flexible. Architects can create custom designs, or you can choose from numerous plans offered by modular manufacturers. Styles range from traditional to ultra-modern.
-
- Strength: Modules are built to withstand the rigours of transportation. They must be lifted by a crane and travel on highways. This requires a resilient structure, often stronger than some site-built equivalents. Bolting them together creates a very solid home.
- Sustainability: The factory setting allows for better waste management and recycling of materials. Precise cutting reduces scrap. Tighter construction improves energy efficiency, lowering heating and cooling costs. Some factories also use sustainable materials.
-
Building Examples
Modular design isn’t limited to simple boxes. It can achieve remarkable results:
-
-
- Modern Masterpieces: Architects use modules to create stunning, contemporary homes with clean lines, large windows, and open floor plans. Modules can be stacked creatively for multi-story designs.
-
- Charming Cottages: Compact and efficient, modular designs excel at creating cosy, well-designed smaller homes or vacation cabins.
-
- Expansive Family Homes: Large single-storey homes, colonials, and compact pitched-roof homes are commonly built modularly. Modules are joined side-by-side and sometimes stacked to create spacious living areas.
-
- Multi-Family Housing: Modular construction is highly efficient for building apartments, town homes, and student housing, offering speed and consistent quality.
-
- Accessory Dwelling Units (ADUs): Modular construction is ideal for backyard cottages or granny flats, providing a fast and less disruptive way to add living space.
- Complex Shapes: Clever design can combine modules at angles or use non-rectangular modules to create unique shapes that don’t look “boxy.”
-
In Conclusion
Modular home design offers a smart alternative to traditional building. It combines the efficiency and quality control of factory construction with the flexibility and permanence of site-built homes.
By designing the house as a set of interconnected modules built indoors, the process achieves significant advantages: faster construction times, predictable costs, high quality, and strong energy performance. Modern techniques ensure modular homes can be beautiful, customized, and built to last, meeting the same standards as any house on the block.
Frequently Asked Questions:
-
-
- Are modular homes cheaper? Often, yes, but not always drastically. Savings come from faster build time (less labour/financing cost), less material waste, and predictable pricing. The value for the quality is excellent.
-
- Do modular homes look different than a regular house? Not necessarily! Modern modular design offers incredible flexibility. They can look identical to any traditional home style, single-storey homes, colonial, cottage style homes, modern, or have a unique contemporary look. The key is the design chosen.
-
- Are modular homes as strong as regular homes? Yes, and often stronger. Modules must endure transportation stresses, requiring robust construction. Once bolted together on a permanent foundation, they form a very solid structure meeting all local building codes.
-
- How long does it take to build a modular home? The factory build might take 4-12 weeks per module (depending on size/complexity). Site prep and foundation work happen concurrently. Assembly on-site typically takes 1-4 weeks. Overall, it’s usually 30-50% faster than site-built.
-
- Can I customize a modular home? Absolutely! While manufacturers offer plans, customization is a major advantage of modern modular. Work with a modular builder/architect to design a home catered for specific needs, within transportation limits.
-
- What are the financing differences? Financing a modular home is very similar to financing a site-built home. You typically get a standard construction loan that converts to a permanent mortgage once the home is complete and certified. Some lenders specialise in modular construction loans.
-
- Do modular homes depreciate? No. Because they are built to local codes and placed on permanent foundations, modular homes appreciate in value over time, just like traditional site-built homes. This is different from manufactured (mobile) homes.
-
- What about resale value? Resale value is generally comparable to similar site-built homes in the same area. There is typically no distinction on property records or appraisals between a well-built modular home and a site-built home.
- Are there limitations on where I can build? The main limitations relate to transportation access. The route from the factory to the site must accommodate the large trucks and modules. Very narrow roads, low bridges, or steep, winding driveways can pose challenges that need planning. Local zoning rules also apply, just like any build.
-
[/vc_column_text][/vc_column][/vc_row]
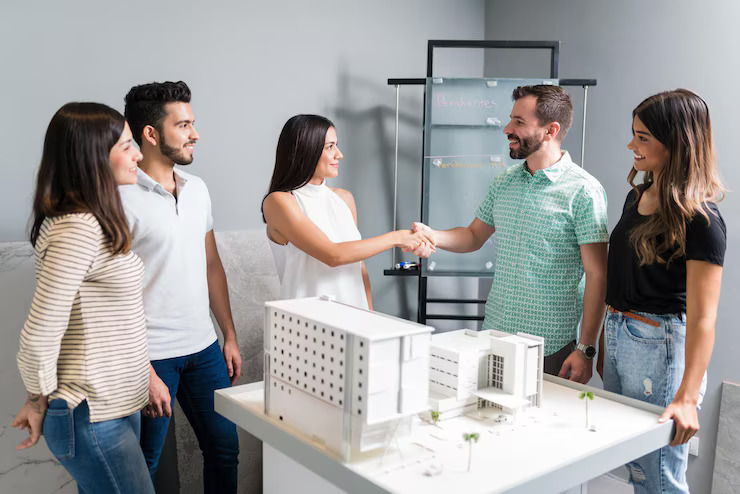
What Are Modular Homes?
A modular home is a house made up of separate sections called modules. These modules are built off-site, usually in a factory. Each module may be a room or a set of rooms. Once complete, the modules are moved to the construction site and placed on a solid foundation.
These are not temporary homes or mobile homes. Modular homes are permanent, just like regular houses built brick by brick on location. They follow the same safety and building codes and often match or even exceed the standards used in conventional construction.
The main idea is to separate the construction into smaller, manageable parts. Instead of building everything at once at the site, the parts are built in a controlled environment and then brought together. This saves time, reduces error, and often lowers costs.
Modular homes can be one-storey or multi-storey. Some are simple and compact. Others are large, with many rooms, porches, and balconies. The outer look can be made to match almost any style: modern, rustic, minimal, or traditional.
From the inside, modular homes are no different. They have kitchens, living rooms, bathrooms, and bedrooms, designed and decorated to the owner’s taste. Once completed, it’s hard to tell that the home wasn’t built on-site from scratch.
Modular Homes v/s Prefabricated Structures
The words “modular” and “prefab” (short for prefabricated) are often used together, sometimes even interchangeably. This can be confusing. It’s helpful to understand that prefab is a broad category. It simply means any part of a building is made before it arrives at the construction site.
Prefab or prefabricated refers to any part of a building that is made off-site. It can include wall panels, roof trusses, or even smaller sections like window frames. Prefab is a broad term. Modular homes fall under this category, but they are a specific kind of prefab construction.
Modular refers to building entire sections of a house; full rooms or parts of rooms in a factory setting. These modules are often built complete with wiring, plumbing, insulation, and flooring. They are transported to the building site and joined together like large building blocks.
Other types of prefabricated structures include:
-
-
- Panelised homes: Walls and floors are built in panels, then assembled on-site.
-
- Pre-cut homes: Materials are pre-measured and cut in a factory but assembled entirely on-site.
- Container homes: Shipping containers are repurposed into housing units.
-
Compared to these, modular homes usually offer better structural strength, faster assembly, and more flexibility in design.
To summarise:
-
-
- All modular homes are prefabricated, but not all prefabricated structures are modular.
-
- Modular homes are delivered in large, mostly complete sections.
- Prefabricated elements can be as small as a window frame or as large as an entire wall. However, the biggest differences between modular and other prefab types, especially manufactured homes, are:
-
-
-
- Building Codes: Modular homes must meet the exact same local and state building codes as traditional site-built homes. They are inspected at the factory and again on-site. Manufactured homes follow the national or regional codes or regulations.
-
- Foundation: Modular homes are placed on a permanent foundation (basement, crawl space, or slab) just like a site-built house. Manufactured homes are often placed on piers or blocks, though they can sometimes be put on a foundation.
-
- Design Flexibility: Modern modular construction offers tremendous design flexibility. While there are practical limits based on transportation, modular homes can look like any traditional house: sleek urban layouts, countryside cottages or multi-storey family homes, even complex modern designs. Manufactured homes often have a recognisable style due to transportation width restrictions.
- Appreciation: Because they meet local codes and are on permanent foundations, modular homes appreciate in value similarly to site-built homes. Manufactured homes typically depreciate, like vehicles.
-
Construction Process of Modular Homes
Understanding how a modular home is built helps explain the design needs. Here’s the typical journey:
-
- Design & Engineering: This is the crucial first step. Architects and engineers work together, often using specialized software. They design the entire house, but broken down into transportable modules.
They determine:
- Design & Engineering: This is the crucial first step. Architects and engineers work together, often using specialized software. They design the entire house, but broken down into transportable modules.
-
-
- Module Size & Shape: How big can each box be to fit on a truck and navigate roads? (Usually max 16 feet wide, 60-70 feet long, but heights vary depending on country and region).
-
- Factory Workflow: How will the module move through the factory assembly line efficiently? What gets installed at each station?
- Approvals: Detailed plans are submitted for local building permits, just like a site-built home.
-
2. Factory Construction:
-
-
- Building the Box: Construction starts on a jig (a precise frame) ensuring perfect dimensions. The floor frame is built first.
-
- Walls Go Up: Exterior and interior walls are framed and stood up on the floor. Sheathing (the outer layer, like plywood) is applied.
-
- Roofing: The roof structure is built and often covered right there in the factory.
-
- Utilities Rough-In: Plumbing pipes and electrical wires are installed inside the walls, floors, and ceilings. HVAC ductwork may also be installed.
-
- Insulation: High-quality insulation is carefully placed in all walls, floors, and ceilings.
-
- Drywall: Interior walls and ceilings get covered with drywall, which is taped, mudded, and sanded smooth.
-
- Interior Finishes: Priming, painting, installing cabinets, countertops, flooring, trim, doors, and even bathroom fixtures often happen in the factory. Appliances might be installed or prepped.
-
- Quality Control: Rigorous inspections happen throughout the process. The finished module is checked against plans.
- Weather Protection: Modules are wrapped tightly for transport to protect against weather and road debris.
-
In many cases, 70–90% of the home is completed before it even leaves the factory.
3. Transportation & Site Prep: While modules are built, the building site is prepared. The foundation (basement, crawl space, or slab) is constructed and inspected. Simultaneously, specialized trucks transport the modules, one or two at a time, to the site. This requires careful route planning.
Proper site preparation ensures that when the modules arrive, everything can be fitted quickly and securely.
4. Crane & Set: A large crane lifts each module off the truck and carefully places it onto the foundation. This is a dramatic and precise operation.
5. Assembly & Finishing:
-
-
- Joining Modules: Modules are bolted together structurally. The roof sections are joined.
-
- Sealing Joints: The seams where modules meet (both inside and outside) are meticulously sealed and flashed to make them weathertight and invisible.
-
- Utility Connections: Electricians and plumbers connect the wiring and plumbing between modules and hook up to the main utilities (septic/sewer, water, electricity, gas).
- HVAC Connections: Ductwork sections between modules are connected, and the system is tested. Skilled workers then handle the sealing, joining, and alignment. This stage is fast; some homes are assembled in just a few days.
-
6. Final Finishes and Inspection
Once assembled, the home undergoes finishing touches. This may include flooring, light fittings, cabinet installations, and paint touch-ups. Then, a final inspection is done to ensure everything meets local building codes. At this point, the home is move-in ready.
Why choose modular? The advantages are compelling:
-
-
- Speed: This is a huge factor. Because factory work happens simultaneously with site prep, and bad weather doesn’t delay indoor construction, the overall build time is significantly faster; often 30-50% quicker than traditional building, that is assuming there are no delays in traditional building due to due to weather, labour shortages, or material supply issues. You move in sooner.
-
- Cost Efficiency: While the base price per square foot might be similar, modular building offers real savings. Faster construction means lower labour costs and financing costs. Less material waste in the controlled factory environment saves money. Predictable pricing is also easier to achieve.
-
- Quality Control: Building in a controlled factory environment is key. Materials are stored properly and protected from weather damage. Skilled workers follow precise processes with constant supervision. Consistent inspections throughout construction ensure high standards. This often results in a tighter, more energy-efficient building envelope.
-
- Scheduling Certainty: Factory production schedules are precise. Weather delays are mostly eliminated. This leads to much greater predictability for move-in dates.
-
- Design Flexibility: Forget the old stereotypes. Modern modular design is highly flexible. Architects can create custom designs, or you can choose from numerous plans offered by modular manufacturers. Styles range from traditional to ultra-modern.
-
- Strength: Modules are built to withstand the rigours of transportation. They must be lifted by a crane and travel on highways. This requires a resilient structure, often stronger than some site-built equivalents. Bolting them together creates a very solid home.
- Sustainability: The factory setting allows for better waste management and recycling of materials. Precise cutting reduces scrap. Tighter construction improves energy efficiency, lowering heating and cooling costs. Some factories also use sustainable materials.
-
Building Examples
Modular design isn’t limited to simple boxes. It can achieve remarkable results:
-
-
- Modern Masterpieces: Architects use modules to create stunning, contemporary homes with clean lines, large windows, and open floor plans. Modules can be stacked creatively for multi-story designs.
-
- Charming Cottages: Compact and efficient, modular designs excel at creating cosy, well-designed smaller homes or vacation cabins.
-
- Expansive Family Homes: Large single-storey homes, colonials, and compact pitched-roof homes are commonly built modularly. Modules are joined side-by-side and sometimes stacked to create spacious living areas.
-
- Multi-Family Housing: Modular construction is highly efficient for building apartments, town homes, and student housing, offering speed and consistent quality.
-
- Accessory Dwelling Units (ADUs): Modular construction is ideal for backyard cottages or granny flats, providing a fast and less disruptive way to add living space.
- Complex Shapes: Clever design can combine modules at angles or use non-rectangular modules to create unique shapes that don’t look “boxy.”
-
In Conclusion
Modular home design offers a smart alternative to traditional building. It combines the efficiency and quality control of factory construction with the flexibility and permanence of site-built homes.
By designing the house as a set of interconnected modules built indoors, the process achieves significant advantages: faster construction times, predictable costs, high quality, and strong energy performance. Modern techniques ensure modular homes can be beautiful, customized, and built to last, meeting the same standards as any house on the block.
Frequently Asked Questions:
-
-
- Are modular homes cheaper? Often, yes, but not always drastically. Savings come from faster build time (less labour/financing cost), less material waste, and predictable pricing. The value for the quality is excellent.
-
- Do modular homes look different than a regular house? Not necessarily! Modern modular design offers incredible flexibility. They can look identical to any traditional home style, single-storey homes, colonial, cottage style homes, modern, or have a unique contemporary look. The key is the design chosen.
-
- Are modular homes as strong as regular homes? Yes, and often stronger. Modules must endure transportation stresses, requiring robust construction. Once bolted together on a permanent foundation, they form a very solid structure meeting all local building codes.
-
- How long does it take to build a modular home? The factory build might take 4-12 weeks per module (depending on size/complexity). Site prep and foundation work happen concurrently. Assembly on-site typically takes 1-4 weeks. Overall, it’s usually 30-50% faster than site-built.
-
- Can I customize a modular home? Absolutely! While manufacturers offer plans, customization is a major advantage of modern modular. Work with a modular builder/architect to design a home catered for specific needs, within transportation limits.
-
- What are the financing differences? Financing a modular home is very similar to financing a site-built home. You typically get a standard construction loan that converts to a permanent mortgage once the home is complete and certified. Some lenders specialise in modular construction loans.
-
- Do modular homes depreciate? No. Because they are built to local codes and placed on permanent foundations, modular homes appreciate in value over time, just like traditional site-built homes. This is different from manufactured (mobile) homes.
-
- What about resale value? Resale value is generally comparable to similar site-built homes in the same area. There is typically no distinction on property records or appraisals between a well-built modular home and a site-built home.
- Are there limitations on where I can build? The main limitations relate to transportation access. The route from the factory to the site must accommodate the large trucks and modules. Very narrow roads, low bridges, or steep, winding driveways can pose challenges that need planning. Local zoning rules also apply, just like any build.
-
[/vc_column_text][/vc_column][/vc_row]
A Step-by-Step Approach to Planning Modern Modular Living Spaces
When the term “modular homes” comes up, it may bring to mind something ultra-modern, quick to build, and ready to live in. And while all that is true, modular homes are more than just fast and efficient; they’re a smart way to build, designed with precision and purpose
Modular homes are often fast and convenient; but they are much more than just a quick housing solution. They represent a smart, efficient, and often surprisingly customizable way to build high-quality houses. But how does one actually design such a home?
Designing a modular home focuses on creating the house as a set of individual sections, built indoors. These modules must fit together perfectly on-site and be strong enough for transportation. Designers carefully plan the module sizes, connections, and overall layout from the very beginning. Designing a successful modular home requires specialized expertise – balancing creativity with the precision of factory construction, transportation logistics, and on-site assembly. AAA-Dubai specializes in crafting innovative modular home designs tailored to modern lifestyles. By combining architectural expertise with cutting-edge technology, they deliver smart, space-efficient solutions that are both stylish and sustainable.
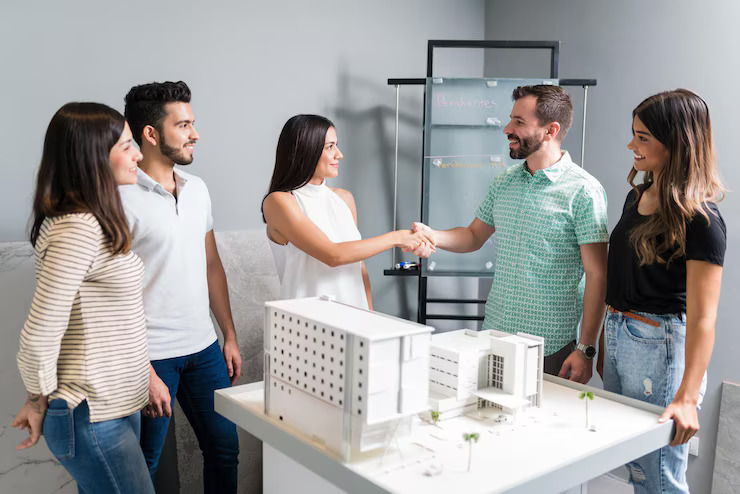
What Are Modular Homes?
A modular home is a house made up of separate sections called modules. These modules are built off-site, usually in a factory. Each module may be a room or a set of rooms. Once complete, the modules are moved to the construction site and placed on a solid foundation.
These are not temporary homes or mobile homes. Modular homes are permanent, just like regular houses built brick by brick on location. They follow the same safety and building codes and often match or even exceed the standards used in conventional construction.
The main idea is to separate the construction into smaller, manageable parts. Instead of building everything at once at the site, the parts are built in a controlled environment and then brought together. This saves time, reduces error, and often lowers costs.
Modular homes can be one-storey or multi-storey. Some are simple and compact. Others are large, with many rooms, porches, and balconies. The outer look can be made to match almost any style: modern, rustic, minimal, or traditional.
From the inside, modular homes are no different. They have kitchens, living rooms, bathrooms, and bedrooms, designed and decorated to the owner’s taste. Once completed, it’s hard to tell that the home wasn’t built on-site from scratch.
Modular Homes v/s Prefabricated Structures
The words “modular” and “prefab” (short for prefabricated) are often used together, sometimes even interchangeably. This can be confusing. It’s helpful to understand that prefab is a broad category. It simply means any part of a building is made before it arrives at the construction site.
Prefab or prefabricated refers to any part of a building that is made off-site. It can include wall panels, roof trusses, or even smaller sections like window frames. Prefab is a broad term. Modular homes fall under this category, but they are a specific kind of prefab construction.
Modular refers to building entire sections of a house; full rooms or parts of rooms in a factory setting. These modules are often built complete with wiring, plumbing, insulation, and flooring. They are transported to the building site and joined together like large building blocks.
Other types of prefabricated structures include:
-
-
- Panelised homes: Walls and floors are built in panels, then assembled on-site.
-
- Pre-cut homes: Materials are pre-measured and cut in a factory but assembled entirely on-site.
- Container homes: Shipping containers are repurposed into housing units.
-
Compared to these, modular homes usually offer better structural strength, faster assembly, and more flexibility in design.
To summarise:
-
-
- All modular homes are prefabricated, but not all prefabricated structures are modular.
-
- Modular homes are delivered in large, mostly complete sections.
- Prefabricated elements can be as small as a window frame or as large as an entire wall. However, the biggest differences between modular and other prefab types, especially manufactured homes, are:
-
-
-
- Building Codes: Modular homes must meet the exact same local and state building codes as traditional site-built homes. They are inspected at the factory and again on-site. Manufactured homes follow the national or regional codes or regulations.
-
- Foundation: Modular homes are placed on a permanent foundation (basement, crawl space, or slab) just like a site-built house. Manufactured homes are often placed on piers or blocks, though they can sometimes be put on a foundation.
-
- Design Flexibility: Modern modular construction offers tremendous design flexibility. While there are practical limits based on transportation, modular homes can look like any traditional house: sleek urban layouts, countryside cottages or multi-storey family homes, even complex modern designs. Manufactured homes often have a recognisable style due to transportation width restrictions.
- Appreciation: Because they meet local codes and are on permanent foundations, modular homes appreciate in value similarly to site-built homes. Manufactured homes typically depreciate, like vehicles.
-
Construction Process of Modular Homes
Understanding how a modular home is built helps explain the design needs. Here’s the typical journey:
-
- Design & Engineering: This is the crucial first step. Architects and engineers work together, often using specialized software. They design the entire house, but broken down into transportable modules.
They determine:
- Design & Engineering: This is the crucial first step. Architects and engineers work together, often using specialized software. They design the entire house, but broken down into transportable modules.
-
-
- Module Size & Shape: How big can each box be to fit on a truck and navigate roads? (Usually max 16 feet wide, 60-70 feet long, but heights vary depending on country and region).
-
- Factory Workflow: How will the module move through the factory assembly line efficiently? What gets installed at each station?
- Approvals: Detailed plans are submitted for local building permits, just like a site-built home.
-
2. Factory Construction:
-
-
- Building the Box: Construction starts on a jig (a precise frame) ensuring perfect dimensions. The floor frame is built first.
-
- Walls Go Up: Exterior and interior walls are framed and stood up on the floor. Sheathing (the outer layer, like plywood) is applied.
-
- Roofing: The roof structure is built and often covered right there in the factory.
-
- Utilities Rough-In: Plumbing pipes and electrical wires are installed inside the walls, floors, and ceilings. HVAC ductwork may also be installed.
-
- Insulation: High-quality insulation is carefully placed in all walls, floors, and ceilings.
-
- Drywall: Interior walls and ceilings get covered with drywall, which is taped, mudded, and sanded smooth.
-
- Interior Finishes: Priming, painting, installing cabinets, countertops, flooring, trim, doors, and even bathroom fixtures often happen in the factory. Appliances might be installed or prepped.
-
- Quality Control: Rigorous inspections happen throughout the process. The finished module is checked against plans.
- Weather Protection: Modules are wrapped tightly for transport to protect against weather and road debris.
-
In many cases, 70–90% of the home is completed before it even leaves the factory.
3. Transportation & Site Prep: While modules are built, the building site is prepared. The foundation (basement, crawl space, or slab) is constructed and inspected. Simultaneously, specialized trucks transport the modules, one or two at a time, to the site. This requires careful route planning.
Proper site preparation ensures that when the modules arrive, everything can be fitted quickly and securely.
4. Crane & Set: A large crane lifts each module off the truck and carefully places it onto the foundation. This is a dramatic and precise operation.
5. Assembly & Finishing:
-
-
- Joining Modules: Modules are bolted together structurally. The roof sections are joined.
-
- Sealing Joints: The seams where modules meet (both inside and outside) are meticulously sealed and flashed to make them weathertight and invisible.
-
- Utility Connections: Electricians and plumbers connect the wiring and plumbing between modules and hook up to the main utilities (septic/sewer, water, electricity, gas).
- HVAC Connections: Ductwork sections between modules are connected, and the system is tested. Skilled workers then handle the sealing, joining, and alignment. This stage is fast; some homes are assembled in just a few days.
-
6. Final Finishes and Inspection
Once assembled, the home undergoes finishing touches. This may include flooring, light fittings, cabinet installations, and paint touch-ups. Then, a final inspection is done to ensure everything meets local building codes. At this point, the home is move-in ready.
Why choose modular? The advantages are compelling:
-
-
- Speed: This is a huge factor. Because factory work happens simultaneously with site prep, and bad weather doesn’t delay indoor construction, the overall build time is significantly faster; often 30-50% quicker than traditional building, that is assuming there are no delays in traditional building due to due to weather, labour shortages, or material supply issues. You move in sooner.
-
- Cost Efficiency: While the base price per square foot might be similar, modular building offers real savings. Faster construction means lower labour costs and financing costs. Less material waste in the controlled factory environment saves money. Predictable pricing is also easier to achieve.
-
- Quality Control: Building in a controlled factory environment is key. Materials are stored properly and protected from weather damage. Skilled workers follow precise processes with constant supervision. Consistent inspections throughout construction ensure high standards. This often results in a tighter, more energy-efficient building envelope.
-
- Scheduling Certainty: Factory production schedules are precise. Weather delays are mostly eliminated. This leads to much greater predictability for move-in dates.
-
- Design Flexibility: Forget the old stereotypes. Modern modular design is highly flexible. Architects can create custom designs, or you can choose from numerous plans offered by modular manufacturers. Styles range from traditional to ultra-modern.
-
- Strength: Modules are built to withstand the rigours of transportation. They must be lifted by a crane and travel on highways. This requires a resilient structure, often stronger than some site-built equivalents. Bolting them together creates a very solid home.
- Sustainability: The factory setting allows for better waste management and recycling of materials. Precise cutting reduces scrap. Tighter construction improves energy efficiency, lowering heating and cooling costs. Some factories also use sustainable materials.
-
Building Examples
Modular design isn’t limited to simple boxes. It can achieve remarkable results:
-
-
- Modern Masterpieces: Architects use modules to create stunning, contemporary homes with clean lines, large windows, and open floor plans. Modules can be stacked creatively for multi-story designs.
-
- Charming Cottages: Compact and efficient, modular designs excel at creating cosy, well-designed smaller homes or vacation cabins.
-
- Expansive Family Homes: Large single-storey homes, colonials, and compact pitched-roof homes are commonly built modularly. Modules are joined side-by-side and sometimes stacked to create spacious living areas.
-
- Multi-Family Housing: Modular construction is highly efficient for building apartments, town homes, and student housing, offering speed and consistent quality.
-
- Accessory Dwelling Units (ADUs): Modular construction is ideal for backyard cottages or granny flats, providing a fast and less disruptive way to add living space.
- Complex Shapes: Clever design can combine modules at angles or use non-rectangular modules to create unique shapes that don’t look “boxy.”
-
In Conclusion
Modular home design offers a smart alternative to traditional building. It combines the efficiency and quality control of factory construction with the flexibility and permanence of site-built homes.
By designing the house as a set of interconnected modules built indoors, the process achieves significant advantages: faster construction times, predictable costs, high quality, and strong energy performance. Modern techniques ensure modular homes can be beautiful, customized, and built to last, meeting the same standards as any house on the block.
Frequently Asked Questions:
-
-
- Are modular homes cheaper? Often, yes, but not always drastically. Savings come from faster build time (less labour/financing cost), less material waste, and predictable pricing. The value for the quality is excellent.
-
- Do modular homes look different than a regular house? Not necessarily! Modern modular design offers incredible flexibility. They can look identical to any traditional home style, single-storey homes, colonial, cottage style homes, modern, or have a unique contemporary look. The key is the design chosen.
-
- Are modular homes as strong as regular homes? Yes, and often stronger. Modules must endure transportation stresses, requiring robust construction. Once bolted together on a permanent foundation, they form a very solid structure meeting all local building codes.
-
- How long does it take to build a modular home? The factory build might take 4-12 weeks per module (depending on size/complexity). Site prep and foundation work happen concurrently. Assembly on-site typically takes 1-4 weeks. Overall, it’s usually 30-50% faster than site-built.
-
- Can I customize a modular home? Absolutely! While manufacturers offer plans, customization is a major advantage of modern modular. Work with a modular builder/architect to design a home catered for specific needs, within transportation limits.
-
- What are the financing differences? Financing a modular home is very similar to financing a site-built home. You typically get a standard construction loan that converts to a permanent mortgage once the home is complete and certified. Some lenders specialise in modular construction loans.
-
- Do modular homes depreciate? No. Because they are built to local codes and placed on permanent foundations, modular homes appreciate in value over time, just like traditional site-built homes. This is different from manufactured (mobile) homes.
-
- What about resale value? Resale value is generally comparable to similar site-built homes in the same area. There is typically no distinction on property records or appraisals between a well-built modular home and a site-built home.
- Are there limitations on where I can build? The main limitations relate to transportation access. The route from the factory to the site must accommodate the large trucks and modules. Very narrow roads, low bridges, or steep, winding driveways can pose challenges that need planning. Local zoning rules also apply, just like any build.
-